The automobile brake drum castings produced by the iron mold sand covering casting process overcome the shortcomings of traditional casting processes and fully utilize the characteristics of the iron mold sand covering rapid cooling process. The iron mold sand covering gray cast iron parts have a dense structure and high mechanical properties. The cooling and solidification conditions of the iron mold sand covering gray cast iron parts are good, and the products have no internal casting defects. Especially for products such as automobile brake drums that require wear resistance and thermal conductivity during use, high carbon can be achieved High strength and hardness can improve the service life of brake drum products. The automotive brake drum product produced by a certain iron mold sand coating process has batch outer circle casting defects, which are mainly concentrated at the upper corner of the large outer circle of the brake drum product. Generally, after machining 1-2 mm, they will be exposed, and in severe cases, there will be obvious holes on the blank. The product’s outer circle is irregularly dense and continuous, as shown in Figure 1. The location of casting defects is distributed in a circular direction.
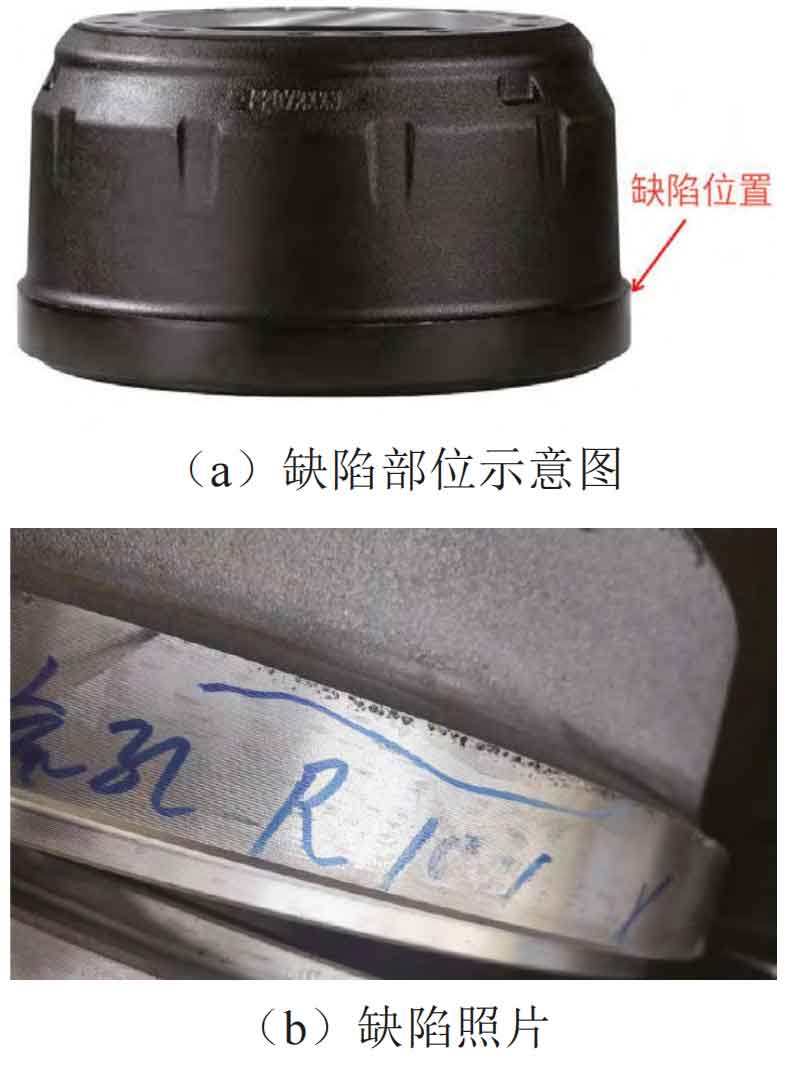
1. Iron mold sand covered casting process
1.1 Melting and molding process
The production of iron mold sand covered casting adopts a medium frequency induction furnace, which uses recycled material, scrap steel and carburizing agent to synthesize cast iron smelting method. The proportion of scrap steel added is 60%~70%, and the rest is recycled material. The recycled material includes sprue, machine added iron chips, and scrap. Carburizing agent uses graphitized carburizing agent, with a fixed C (mass fraction) greater than 98% ω (S) ≤ 0.5%, ash content ≤ 2%, volatile content ≤ 1%, particle size 1-5 mm. The order of adding furnace materials is to add 50% recycled material (iron filings) to the bottom of the furnace, then add 70% carburizing agent and scrap steel. During the process of adding scrap steel, the remaining 30% carburizing agent is divided into two parts and added to the furnace. In order to improve the absorption rate of the carburizing agent, the carburizing agent is added in three parts during the feeding process. This will ensure that a high carbon melt pool is quickly formed at the bottom of the electric furnace after power supply, which reduces the melting point of the scrap steel due to surface carbonization and plays a melting aid role [4]. The melting temperature of molten iron is 1500~1530 ℃, and it is allowed to stand at high temperature for 5 minutes at 1530~1550 ℃ and repeatedly scrape the slag. The temperature for molten iron to be produced from the furnace is 1490-1530 ℃. During casting, 75 # silicon iron is used for inoculation treatment. The final casting temperature is not lower than 1360 ℃, and the entire casting time for the package is not more than 15 minutes.
The old sand is made of recycled coated sand, while the new sand is made of Inner Mongolia Tongliao sand with a particle size of 70-140 mesh. The amount of new sand added is 5% -20%, and the rest is recycled sand. The coated sand adopts a thermal regeneration process, which mainly includes: old sand crushing → screening → magnetic separation → thermal regeneration → removal of micro powder → cooling → storage → inspection and other processes. The room temperature tensile strength of coated sand is ≥ 2.5 MPa, the room temperature bending strength is ≥ 6 MPa, the normal hot tensile strength is ≥ 1.3 MPa, the hot bending strength is ≥ 3.8 MPa, the ignition reduction is ≤ 2.6%, the gas generation is ≤ 20 mL, and the melting point is 95-110 ℃.
1.2 Pouring system
The pouring system is shown in Figure 2, using the middle top pouring method. The pouring cup adopts a funnel-shaped shape, and the pressure angle formed by the top of the cup and the maximum outer circle on the surface of the iron mold covered with sand gray cast iron is not less than 40 °. A 15 PPI ceramic filter is placed inside the pouring cup to filter the iron liquid. A pouring groove of no less than R50 is set below the pouring cup to buffer the iron liquid entering the mold cavity and avoid high turbulence of the iron liquid. Adopting a semi enclosed pouring system, Σ Within S: Σ S horizontal: Σ S straight=1:4.17:2.04, set up 4 or 5 inner gates according to the product structure, with a single inner gate cross-sectional area of no less than 240 mm ^ 2. The single pouring time of iron mold sand covered gray cast iron parts shall not exceed 25 seconds, and two stress grooves shall be set on both sides of the inner gate to play a fracture role in removing the pouring system and protect the iron mold sand covered gray cast iron parts from damage. The width of the transverse sprue is consistent with the width of the inner sprue, and the thickness is determined based on the flange wall thickness of the iron mold covered with sand gray cast iron. Generally, it is set at 1.25 times the flange wall thickness to ensure that the metal liquid flows into the inner sprue in a sufficient and stable manner. At the same time, the low-temperature metal liquid containing gas and slag initially poured is stored to prevent slag.
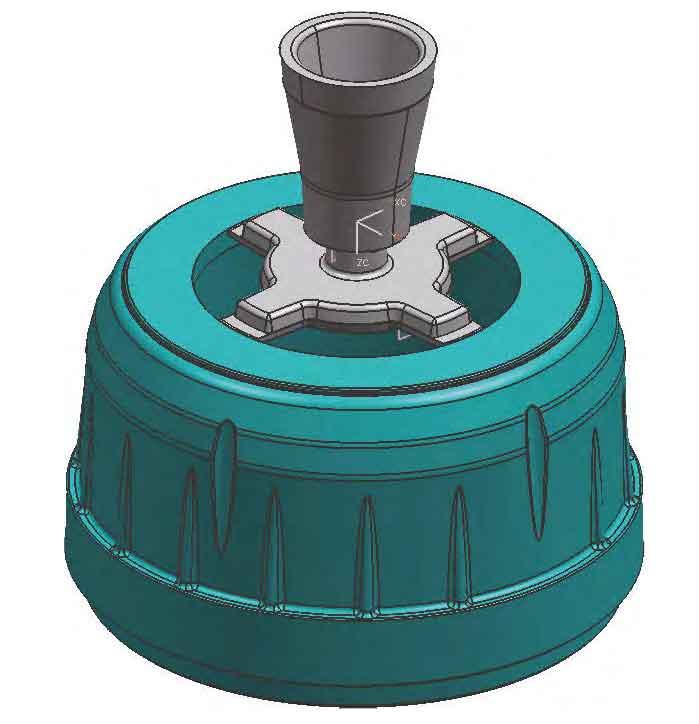
2. Analysis of defects in iron mold sand covered casting
2.1 EDS spectrum analysis
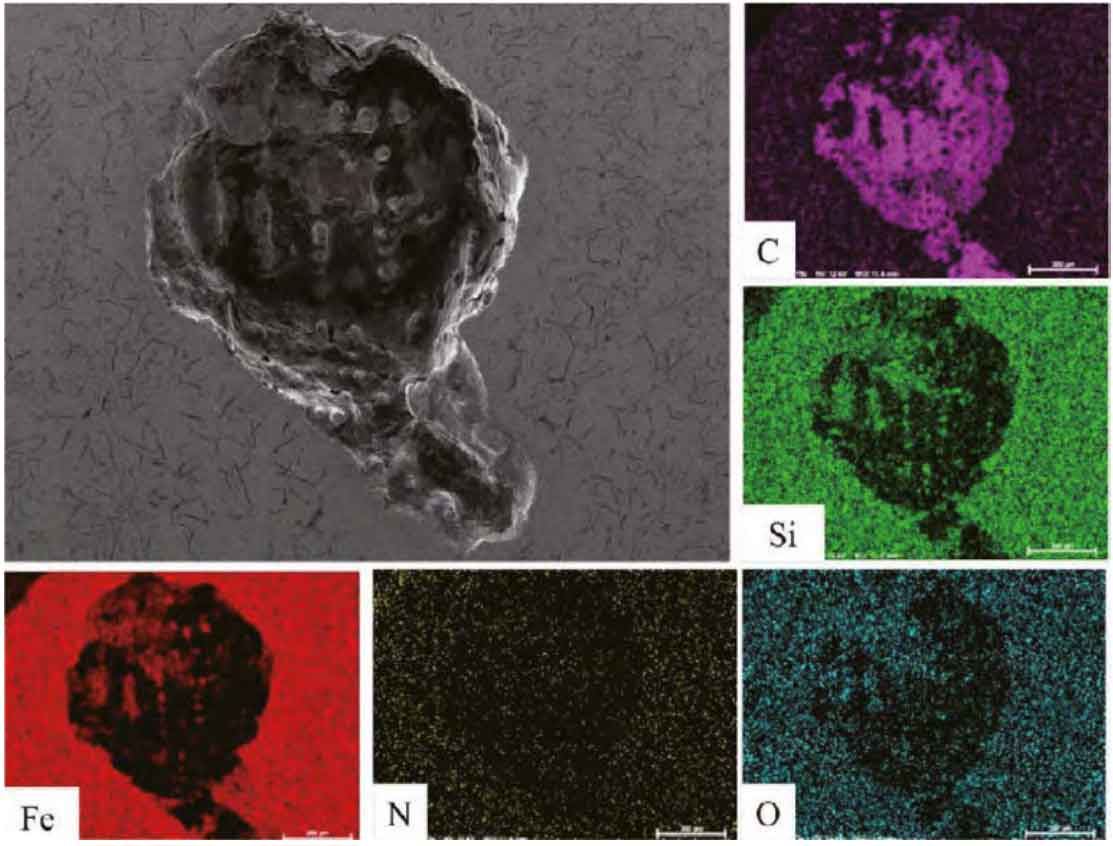
EDS energy spectrometer was used to analyze the casting defects and their surroundings. From the scanning image of the casting defect surface, it can be seen that there are milky dendrites in the casting defect area, and the shape of the casting defect is irregular. It is perpendicular to the surface of the iron mold sand covered gray cast iron and penetrates 2-5 mm deep into the iron mold sand covered gray cast iron. As shown in Figure 3, the defect area of the iron mold sand covered gray cast iron is mainly composed of elements such as C, N, Fe, O, and Si, among which N, C The content of the three elements Fe is relatively high, as shown in Table, and segregation occurs, but the content inside and outside the casting defect is different. The detection results indicate that C element is mainly enriched inside the casting defect, while N element is mainly distributed in the area around the casting defect, and the distribution is relatively uniform. It can be clearly seen from Figure 3 that there are continuous or discontinuous graphite film precipitates inside the casting defects, and the surrounding decarburized matrix structure is connected to it. This is a typical nitrogen porosity casting defect caused by high N content.
N | C | Fe | O | Si |
49.5 | 28.58 | 12.71 | 8.87 | 0.34 |
2.2 Mechanism of nitrogen pore formation
The nitrogen in molten iron is dissolved in iron, forming a interstitial solid solution. During the solidification process of molten iron, the solubility of nitrogen also decreases with the decrease of temperature. During the solidification process of molten iron, the solubility of nitrogen in the first solidified molten iron decreases, causing the nitrogen content in the later solidified molten iron to gradually increase. When the nitrogen content in the molten iron exceeds the solubility of the molten iron, nitrogen will precipitate. However, due to the fast cooling speed of the iron mold sand casting process, It can cause the surface iron liquid to solidify and crust, and nitrogen cannot be discharged smoothly, forming nitrogen porosity casting defects.
2.3 Analysis of the causes of nitrogen stomata
The reason for the formation of nitrogen pores is in the molten iron ω (N) Due to excessive temperature, for iron mold sand covered gray cast iron brake drum castings, when in the molten iron ω (N) When it exceeds 120 ppm, nitrogen pores are prone to occur, and the main sources of nitrogen are as follows:
(1) Scrap steel: Synthetic cast iron uses a relatively high proportion of scrap steel during smelting, and scrap steel, especially ordinary carbon steel, high manganese steel, and other gray cast iron castings with high demand for scrap steel ω (N) They are all relatively high, such as low-carbon steel ω (N) Approximately 40-60 ppm, threaded steel ω (N) Approximately 90 ppm, rail steel ω (N) Approximately 110-120 ppm.
(2) Carburizing agent: Coal based carbonizing agent ω (N) Approximately 2000~7000 ppm, i.e. 0.2%~0.7%; Carbon enhancing agent for ordinary calcined petroleum coke ω (N) Generally around 1000 ppm; High temperature calcined petroleum coke carbonization agent ω (N) 300-500 ppm; Graphitized carburetor ω (N) Not exceeding 300 ppm.
(3) Coated sand: Coated sand mainly consists of raw sand, recycled sand, thermoplastic phenolic resin, curing agent, and additives. The widely used curing agent in the industry is Ulotopine, which will decompose significantly when heated at 230 ℃ or above. Therefore, during the heating, curing, and pouring process of coated sand, a large amount of NH3 will be released.
By detecting the nitrogen content in the molten iron, it was measured to be 71.7 ppm, which is not enough to cause nitrogen porosity in the iron mold covered with sand gray cast iron. Therefore, we have ruled out the factors that cause nitrogen porosity casting defects due to excessive nitrogen content in the molten iron. In the formula of coated sand produced, the amount of resin added accounts for 2%~2.5% of the mass fraction of the original sand. Among them, urotropine accounts for 15% of the resin mass, and N accounts for 40% of its mass in urotropine. After calculation, the amount of resin added in coated sand ω (N) About 0.12%~0.15%, far exceeding the aforementioned 120 ppm, may cause nitrogen porosity casting defects in iron mold coated gray cast iron parts.
3. Improvement measures
3.1 Quality improvement of coated sand
(1) Change the supplier of raw materials for coated sand, especially ensuring the quality of thermoplastic phenolic resin and urotropine.
(2) Increase the amount of new sand added in the proportion of coated sand, from the current 5% -20% to 20% -40%, to reduce the residual nitrogen content in recycled sand and reduce the risk of nitrogen porosity.
(3) Distinguish and manage the use of recycled old sand for shell and iron production lines. Due to the different performance requirements, sand particle size, and new sand addition of the two production lines, the mixing of recycled sand can lead to process problems.
3.2 Production process improvement
Based on the production process characteristics of iron mold sand coating casting, the following improvements have been made in process control due to the high N content of coated sand:
(1) Adding exhaust plugs to the mold, especially at the bottom and corners, is beneficial for the gas discharge during the solidification of the coated sand, while also facilitating the filling of the coated sand and improving the quality of sand injection.
(2) Ulotopine in coated sand will decompose significantly at 230 ℃, while the solidification temperature of iron mold coated sand is generally 220-240 ℃. Therefore, the mold temperature is set to 230-250 ℃ and the iron mold temperature is set to 240-280 ℃ to accelerate the gas generation of coated sand.
(3) To remove the volatile gas from the coated sand inside the mold cavity, the number of iron mold exhaust channels has been increased from 8 to 20. At the same time, the time from the solidification of the box to the start of pouring is extended from 10 minutes to no less than 20 minutes, which is conducive to the discharge of gas.
(4) Appropriately increasing the pouring temperature and reducing the viscosity of the molten iron are beneficial for the upward migration of gas invading the molten iron, thereby reducing the formation of porosity casting defects in gray cast iron castings with sand coating on the iron mold.
4. Conclusion
By adjusting and distinguishing the suppliers of raw materials for coated sand and recycled old sand, the proportion of new sand added in the mixed sand ratio was adjusted to 20%~40%. At the same time, exhaust channels for molds and iron molds were added. Measures such as increasing iron mold temperature, curing time, and pouring temperature were taken in the production process, and more than 100000 products were continuously produced without nitrogen porosity casting defects.