Sand casting is a versatile and widely used manufacturing process that enables the production of complex metal parts. Optimizing sand casting parts for high-performance applications involves a thorough understanding of material properties, process parameters, and quality control measures. This article delves into the various strategies and techniques employed to enhance the performance and reliability of sand casting parts in demanding applications.
Introduction to Sand Casting
Sand casting is a process where molten metal is poured into a sand mold to create a metal part. The process is popular due to its ability to produce large, complex shapes and its cost-effectiveness. However, optimizing sand casting parts for high-performance applications requires careful consideration of various factors, including material selection, mold design, and process control.
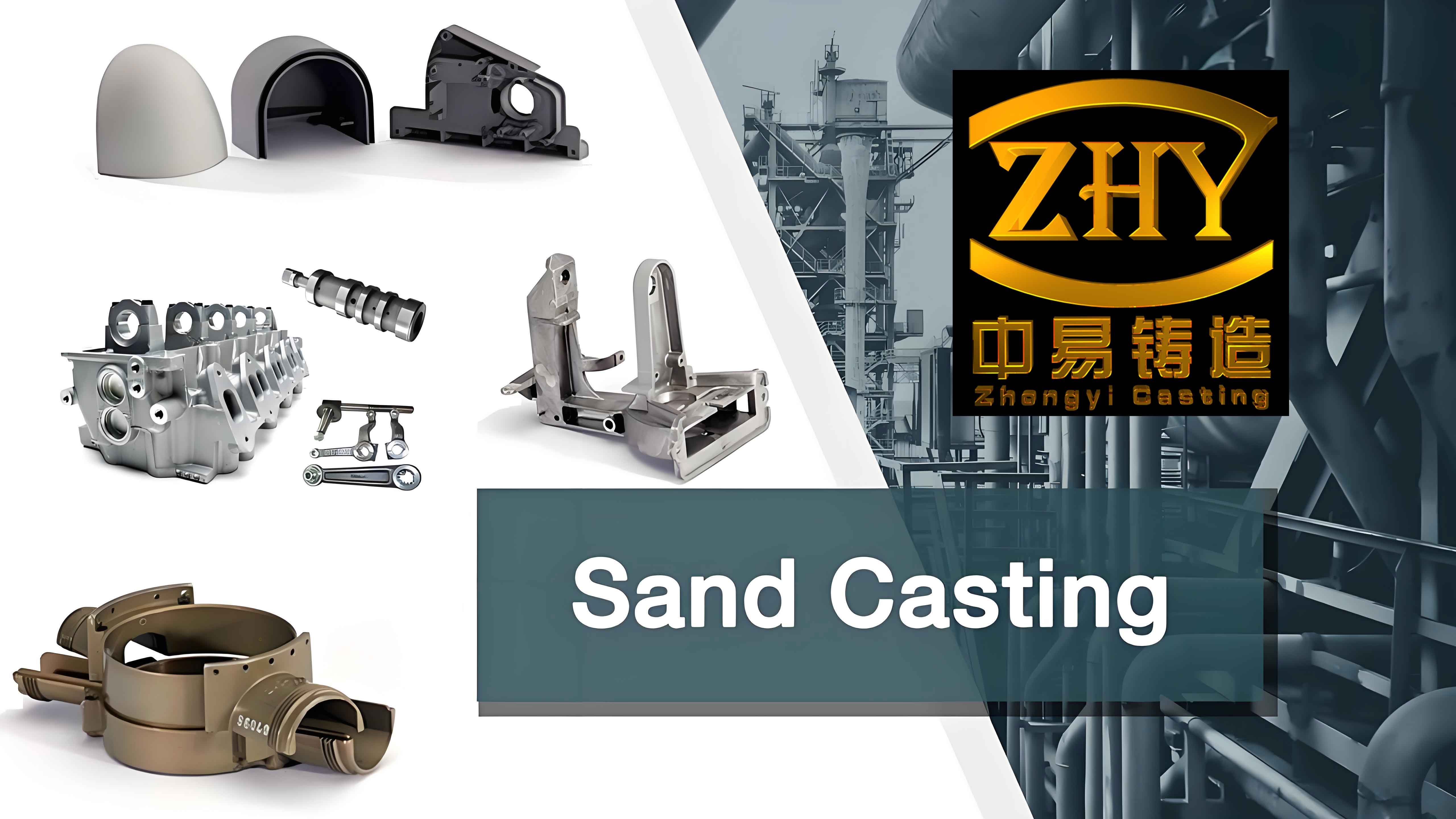
Material Selection for High-Performance Sand Casting Parts
Selecting the right material is crucial for the performance of sand casting parts. The material must possess the necessary mechanical properties to withstand the intended application.
Common Materials Used in Sand Casting
- Gray Cast Iron
- Applications: Engine blocks, machine bases, pipes
- Benefits: Good machinability, excellent vibration damping
- Ductile Iron
- Applications: Automotive components, agricultural machinery
- Benefits: High strength, good toughness, wear resistance
- Aluminum Alloys
- Applications: Aerospace components, automotive parts
- Benefits: Lightweight, good corrosion resistance, excellent thermal conductivity
- Steel Alloys
- Applications: Structural components, heavy machinery
- Benefits: High strength, durability, and wear resistance
Table 1: Comparison of Common Materials
Material | Applications | Benefits |
---|---|---|
Gray Cast Iron | Engine blocks, machine bases, pipes | Good machinability, excellent vibration damping |
Ductile Iron | Automotive components, agricultural machinery | High strength, good toughness, wear resistance |
Aluminum Alloys | Aerospace components, automotive parts | Lightweight, good corrosion resistance, excellent thermal conductivity |
Steel Alloys | Structural components, heavy machinery | High strength, durability, wear resistance |
Mold Design for Optimizing Sand Casting Parts
The design of the sand mold significantly impacts the quality and performance of the final casting. Advanced mold design techniques can minimize defects and ensure the structural integrity of the cast parts.
Key Considerations in Mold Design
- Pattern Design
- Precision: Ensuring the pattern accurately reflects the desired dimensions and geometry of the final part.
- Draft Angles: Incorporating appropriate draft angles to facilitate easy removal of the pattern from the mold.
- Gating System
- Design: Designing an effective gating system to ensure smooth and controlled flow of molten metal into the mold.
- Location: Strategically placing gates to minimize turbulence and prevent defects such as inclusions and cold shuts.
- Riser Placement
- Function: Ensuring proper riser placement to compensate for metal shrinkage during solidification.
- Efficiency: Optimizing the size and location of risers to reduce material waste and improve yield.
- Cooling Rate Control
- Importance: Controlling the cooling rate to avoid thermal stresses and ensure uniform solidification.
- Techniques: Using chill blocks or varying mold materials to achieve the desired cooling rates.
Table 2: Mold Design Elements and Their Impact
Element | Impact on Casting Quality |
---|---|
Pattern Design | Ensures dimensional accuracy, reduces defects |
Gating System | Controls metal flow, minimizes turbulence, prevents defects |
Riser Placement | Compensates for shrinkage, improves yield |
Cooling Rate Control | Avoids thermal stresses, ensures uniform solidification |
Process Optimization Techniques
Optimizing the sand casting process involves fine-tuning various parameters to achieve the desired mechanical properties and minimize defects.
Key Process Parameters
- Sand Quality
- Composition: Using high-quality sand with appropriate grain size and binder content.
- Moisture Control: Maintaining optimal moisture levels to ensure mold stability and reduce casting defects.
- Metal Temperature
- Pouring Temperature: Controlling the temperature of the molten metal to ensure proper flow and solidification.
- Superheat: Managing the superheat to avoid premature solidification and ensure complete mold filling.
- Mold Compaction
- Technique: Using proper mold compaction techniques to ensure uniform density and strength of the mold.
- Equipment: Employing advanced molding equipment for consistent and efficient mold preparation.
- Casting Environment
- Temperature Control: Maintaining a stable casting environment to prevent thermal fluctuations.
- Humidity Control: Regulating humidity levels to avoid moisture-related defects in the mold.
List: Process Optimization Techniques
- Sand Quality Control: Ensuring optimal sand composition and moisture levels.
- Precise Temperature Management: Controlling pouring temperature and superheat.
- Advanced Mold Compaction: Using proper techniques and equipment.
- Stable Casting Environment: Regulating temperature and humidity.
Quality Control Measures
Implementing rigorous quality control measures is essential to ensure the reliability and performance of sand casting parts.
Inspection Methods
- Non-Destructive Testing (NDT)
- Ultrasonic Testing: Detects internal defects and assesses material integrity.
- Radiographic Testing: Identifies subsurface defects using X-rays.
- Dimensional Inspection
- Coordinate Measuring Machines (CMM): Ensures dimensional accuracy of the cast parts.
- Laser Scanning: Provides precise measurements and 3D modeling of cast components.
- Mechanical Testing
- Tensile Testing: Measures the tensile strength and elongation of the material.
- Hardness Testing: Assesses the surface hardness and wear resistance of sand casting parts.
List: Quality Control Techniques
- Non-Destructive Testing: Ultrasonic testing, radiographic testing.
- Dimensional Inspection: Coordinate measuring machines, laser scanning.
- Mechanical Testing: Tensile testing, hardness testing.
Conclusion
Optimizing sand casting parts for high-performance applications involves a comprehensive approach that encompasses material selection, mold design, process optimization, and quality control measures. By leveraging advanced techniques and technologies, manufacturers can produce high-quality sand casting parts that meet the stringent demands of industries such as automotive, aerospace, and heavy machinery. Continuous improvements in these areas will further enhance the capabilities and applications of sand casting parts in high-performance manufacturing.