Because of the special solidification property of ductile iron, it is easy to produce shrinkage cavity and shrinkage porosity. How to control and eliminate the shrinkage cavity and porosity of ductile iron has always been a problem of concern to foundry workers, and also a difficult problem in the production of ductile iron castings in the world. Many experts and scholars at home and abroad have made a lot of in-depth research, and put forward some specific measures to eliminate shrinkage cavity and porosity, which has been proved to be effective in production practice. However, due to the complexity of shrinkage cavity and porosity formation of ductile iron, there are still many different views on the formation mechanism and prevention measures of shrinkage cavity and porosity, especially for small and medium nodular iron castings The research on Solidification Characteristics and process parameters of shrinkage cavity and porosity is less and systematic, so it is lack of effective guidance for actual casting production. In China, many nodular iron casting factories rely on experience in casting process design and are blind. Therefore, how to effectively reduce and eliminate shrinkage cavity and porosity of ductile iron is worthy of further study.
Torbjorn of Norway studied the effect of different spheroidizing inoculation methods on the shrinkage porosity of hot metal. Spheroidization is mainly divided into spheroidization in transfer package and spheroidization in mold.
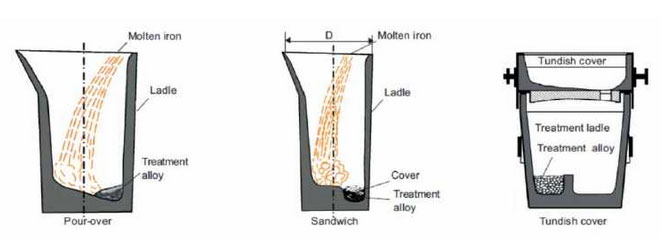
In ladle spheroidizing is to put the spheroidizing agent at the bottom of the transfer ladle, and the spheroidizing agent will not react with it gradually after the molten iron enters, and the spheroidizing steam contacts with the molten iron to spheroidize the molten iron. Fig. 1 according to the different storage position of spheroidizing agent at the bottom of the bag, the inoculation method in the bag can be divided into the flush method, “sandwich” method and capping method. Generally, inoculation treatment is carried out separately after spheroidizing treatment, and hot metal can be inoculated by means of ladle and flow following methods.
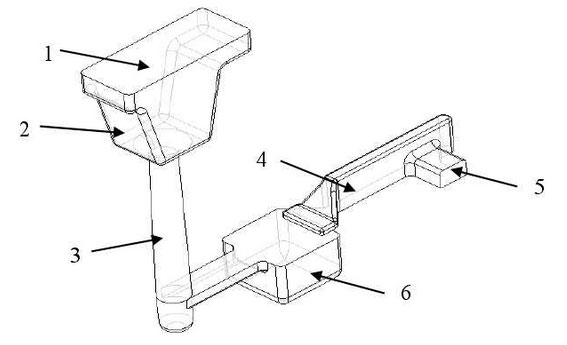
In mold spheroidization means that the spheroidizing reaction occurs in the mold, which is completely different from the inoculation in the ladle. The spheroidizing agent acts as the inoculant at the same time, and the spheroidizing absorption rate can exceed 80% (the spheroidizing absorption rate in the ladle is 0 In mold spheroidizing casting can significantly reduce or completely eliminate the need for annealing. Due to the nucleation effect in the mold, more spheroidal graphite is produced and almost no carbide is formed. Figure 2 is a typical diagram of in mold spheroidization inoculation system. Since the production process of in mold spheroidization is much simpler than that in ladle spheroidization, the processes of slag removal, inoculation, spheroidizing time control and furnace sampling and testing after magnesium addition treatment are canceled, thus greatly improving the production efficiency.
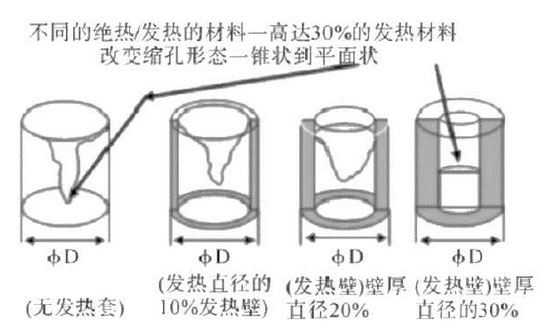
H. roedter of Germany studied how to solve the shrinkage porosity of castings by improving the feeding efficiency of risers. The liquid feeding efficiency of the traditional sand mold riser is only 15% – 30% of the riser weight, but the feeding efficiency of the riser with heating riser sleeve can reach more than 70%. Compared with the outer wall of the sand mold riser, the heat preservation performance of the heating riser sleeve is greatly improved, which is conducive to increasing the temperature of molten iron in the riser, allowing the metal to exist in liquid form for a longer time, thus increasing the effective modulus of the riser and extending the feeding time and distance. Figure 3 shows the utilization rate of metal used for feeding in the heating riser sleeve with different wall thickness. The most effective heating riser available can keep the molten iron in the riser at 1500 ℃ for more than 5 minutes or even longer. The heating riser does not need runner connection, and can save 75% of the volume and greatly improve the yield.