Quality control in lost foam casting is pivotal to achieving high-quality outcomes, particularly given the complexity and intricacy of the parts that this process can produce. Effective quality control techniques can help minimize defects, reduce waste, and ensure that the final products meet all specified requirements. Here are some critical quality control techniques for optimizing outcomes in lost foam casting:
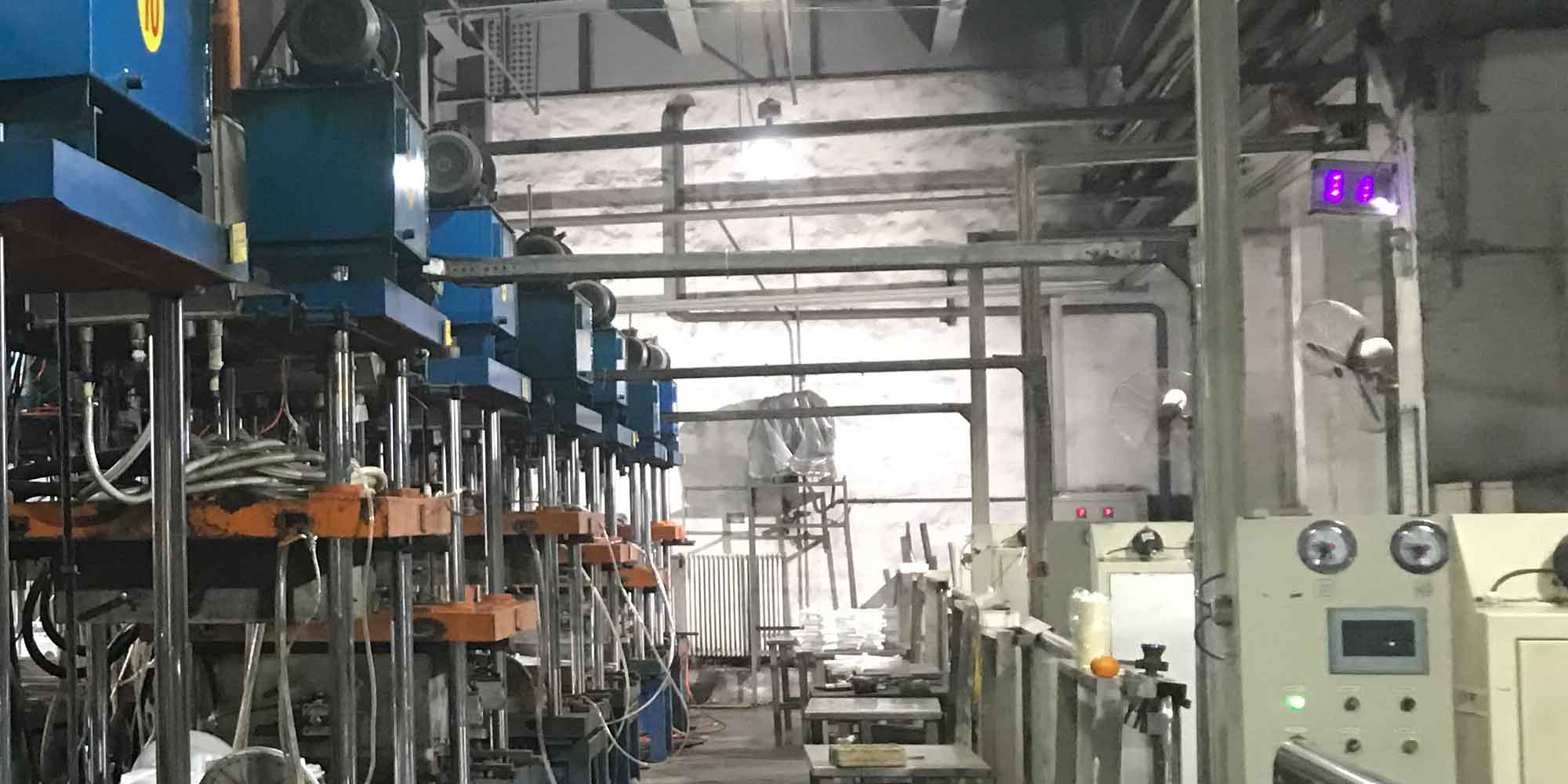
1. Design and Pattern Making
- 3D CAD Modeling: Utilize computer-aided design (CAD) software to create accurate and detailed designs of the parts and the foam patterns. This helps in identifying potential issues in the early stages of the design process.
- Pattern Material and Quality: Ensure the quality and consistency of the foam material used for creating patterns. Any defects in the foam, such as inhomogeneities or impurities, can lead to defects in lost foam casting parts.
2. Mold Preparation and Filling
- Coating Uniformity: The refractory coating applied to the foam pattern must be uniform and free of defects to prevent sand from coming into direct contact with the molten metal, which can cause sand-related defects.
- Vibration Control: During the filling process, ensure proper vibration to help the sand settle uniformly around the pattern. This minimizes the risk of defects such as shifts or gas entrapments.
3. Molten Metal Handling
- Metal Quality and Preparation: Regularly test the quality of the metal to ensure it is free of impurities. The temperature and viscosity of the metal should be precisely controlled to ensure complete filling and solidification without defects.
- Pouring Technique: The pouring technique and rate should be controlled to avoid turbulence and splashing, which can lead to cold shuts and misruns.
4. Cooling and Solidification
- Controlled Cooling: Implement controlled cooling techniques to manage the rate of solidification, which can significantly affect the mechanical properties and internal integrity of lost foam casting parts.
- Temperature Monitoring: Use thermocouples or other temperature-monitoring devices to ensure that the cooling rates are within the desired range to prevent stresses and warping.
5. De-molding and Cleaning
- Gentle Handling: Handle the parts gently during de-molding to avoid damaging lost foam casting.
- Post-processing Inspection: After removing the refractory coating and cleaning lost foam casting parts, conduct a thorough inspection to identify any surface or internal defects.
6. Advanced Non-Destructive Testing (NDT)
- X-Ray and CT Scanning: Use X-ray or computed tomography (CT) scanning to detect internal defects such as porosity, inclusions, or incomplete fusion which are not visible on the surface.
- Ultrasonic Testing: Employ ultrasonic testing for thicker sections where X-rays might not penetrate completely.
7. Dimensional Accuracy
- 3D Scanning: Utilize 3D scanning technology to check the dimensional accuracy of the parts against the CAD models. This helps in detecting deviations early and adjusting the process parameters accordingly.
- CMM (Coordinate Measuring Machine): Use CMM for precise measurement of critical dimensions and tolerances.
8. Statistical Process Control (SPC)
- Data Collection and Analysis: Collect and analyze data from various stages of lost foam casting process. Use SPC techniques to monitor and control the process variables that influence the quality of lost foam casting.
- Feedback Loop: Establish a feedback loop from the quality control data to the production team to continuously improve the process and reduce the occurrence of defects.
9. Employee Training
- Regular Training: Provide regular training for workers and technicians on the latest techniques and technologies in lost foam casting. Educate them about the importance of each step of the process and how it impacts the overall quality of the product.
By implementing these quality control techniques, manufacturers can significantly enhance the reliability and quality of products made through lost foam casting. This not only reduces the rate of defects and rework but also improves customer satisfaction and the overall efficiency of the production process.