The solid-liquid phase transition process changes greatly under pressure. With the increase of the temperature of the solid-liquid phase line, the eutectoid transition point moves to low temperature, the carbon content decreases, and new phases and phase regions appear, which changes the properties of the known phases and the shape of the equilibrium phase diagram.
In addition, due to the decrease of solute diffusion coefficient under high pressure, the solid solubility of elements is greatly expanded, the solute distribution coefficient changes, leading to the instability of solid-liquid interface, the structure and morphology of solidification structure changes, and various non-equilibrium structures can be obtained, even quasicrystal or amorphous can be formed. From the macro point of view, the quality of pressure casting is better than that of sand casting, the internal structure is compact, and the surface quality is close to the forging level, which can obtain better economic benefits.
The semi-solid slurry of hypereutectic high chromium cast iron was obtained by oblique cooling method, and the alloy sample was prepared by pressing in the metal mold. The microstructure of the sample is shown in Fig. 1. Under the pressure of 150 MPa, the size of primary carbide in the solidified structure of the sample becomes smaller, and there is basically no shrinkage cavity. The impact toughness of 150 MPa sample is 121% and 17% higher than that of conventional casting and semi-solid casting respectively, and the wear resistance is 78% and 20% higher than that of conventional casting and semi-solid casting respectively.
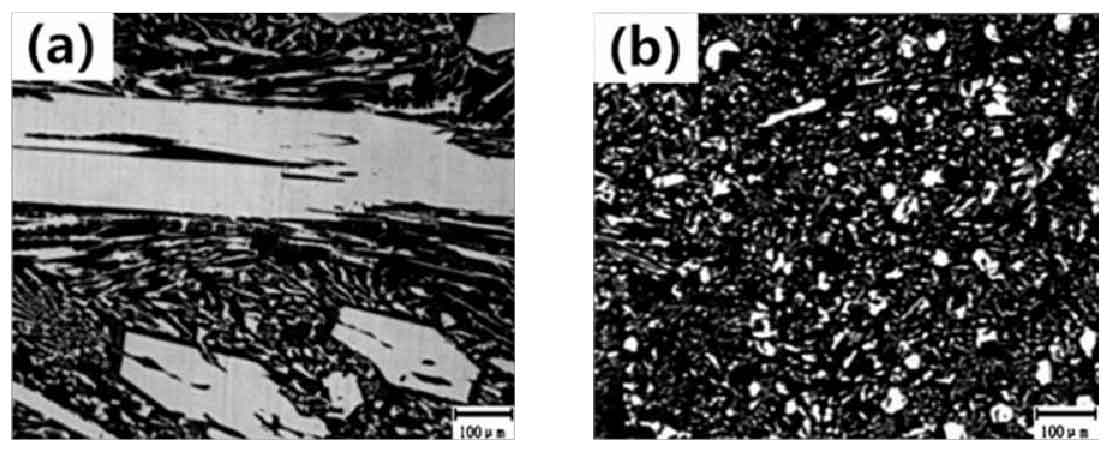
The hypereutectic high chromium cast iron with alloy content of C 4.7 wt% and Cr 23 wt% was prepared by rheo squeeze casting. The solidification structure of the alloy is shown in Figure 2. The larger white block is primary carbide and the smaller one is eutectic carbide. With the increase of pressure from 5MPa to 20MPa, the average cross-sectional area of primary carbides in hypereutectic carbides increases first and then decreases. Compared with 20MPa, the size change of 10MPa is not obvious. Increasing the pressure does not necessarily refine the carbide. Although the pressure reduces the internal defects in the solidified samples, how to select the appropriate pressure to obtain fine primary carbides is the key to obtain the optimal solidification structure.
High chromium cast iron (C 3.3 wt% and Cr 18 wt%) samples were prepared by liquid die forging in Xing Shuming research group. The microstructure is shown in Fig. 3. After characterization, it is found that liquid forging can improve the hardness of high chromium cast iron and make the carbides arrange closely. The amount of carbides per unit area is 3 ~ 5 times as much as that of non pressurized metal mold. When the forging pressure reaches 150MPa, the grain size of the sample increases from 25 to 50 when the forging pressure is not increased μ M is reduced to 10 ~ 25 μ m. The grain size is obviously refined.
The effect of solidification pressure of 0.1, 1 and 2 MPa on the as cast microstructure of M42 high speed steel was studied by Hongchun Zhu. The results show that the cooling rate can be significantly increased by changing the heat transfer coefficient of the interface by increasing the solidification pressure, so that the as cast microstructure of M42 high speed steel can be significantly improved. As shown in Fig. 4, with the increase of pressure, the arm spacing of the first and second dendrites in the solidification structure of the sample decreases, the average thickness of eutectic dendrites decreases, the dendrites are refined, the distribution of eutectic ledeburite is more uniform, the size is smaller, and the morphology of carbides changes from large-size flake and straight rod to Small-size arc rod. In addition, as shown in Fig. 5, with the increase of solidification pressure, the volume fraction of M6C carbide decreases significantly, and the volume fraction of M2C increases accordingly.
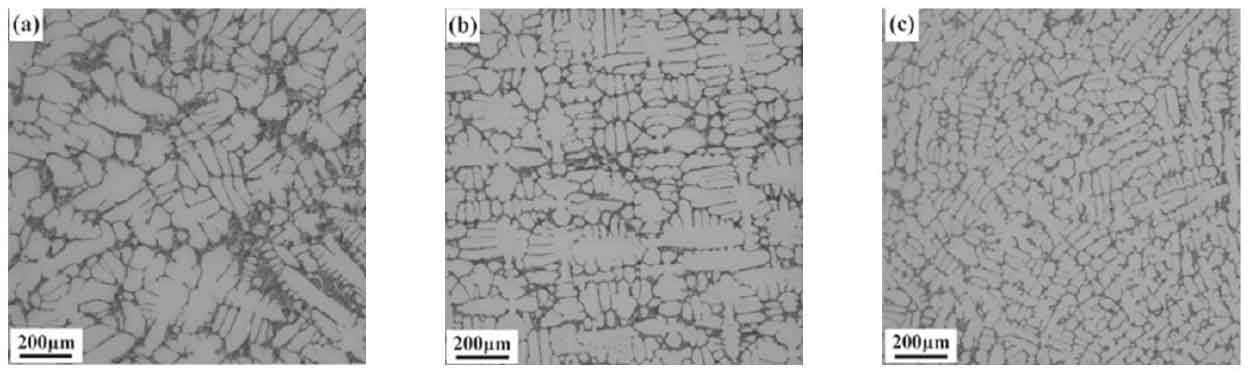
In conclusion, it can be seen that the probability of shrinkage cavity and porosity of Cr based alloy decreases under high pressure, which changes the morphology and size of primary phase and eutectic phase as well as the phase composition of the alloy, thus changing the properties of the alloy. However, the law and mechanism of the change of these structures and properties with different pressure conditions are not very clear, especially for chromium alloys. Most of the existing methods to improve the properties of pressure cast chromium alloys are based on the analysis of the microstructure of the alloys, but the effect of pressure on the solidification behavior of the alloys still needs to be further studied.