Sand casting is widely used manufacturing process that allows for the creation of complex metal parts with a variety of shapes and sizes. However, the surface quality of sand casting parts often needs improvement to meet specific performance and durability requirements. Surface finishing methods play a crucial role in enhancing the durability and overall performance of sand casting parts. This article explores various surface finishing techniques and their impact on the durability of sand casting parts.
Introduction to Sand Casting
Sand casting involves creating a mold from a sand mixture, pouring molten metal into the mold, and allowing it to solidify. The mold is then broken away to reveal the metal part. While sand casting is versatile and cost-effective, the resulting surface of the cast parts can be rough and contain imperfections. To improve the durability and performance of sand casting parts, various surface finishing methods are employed.
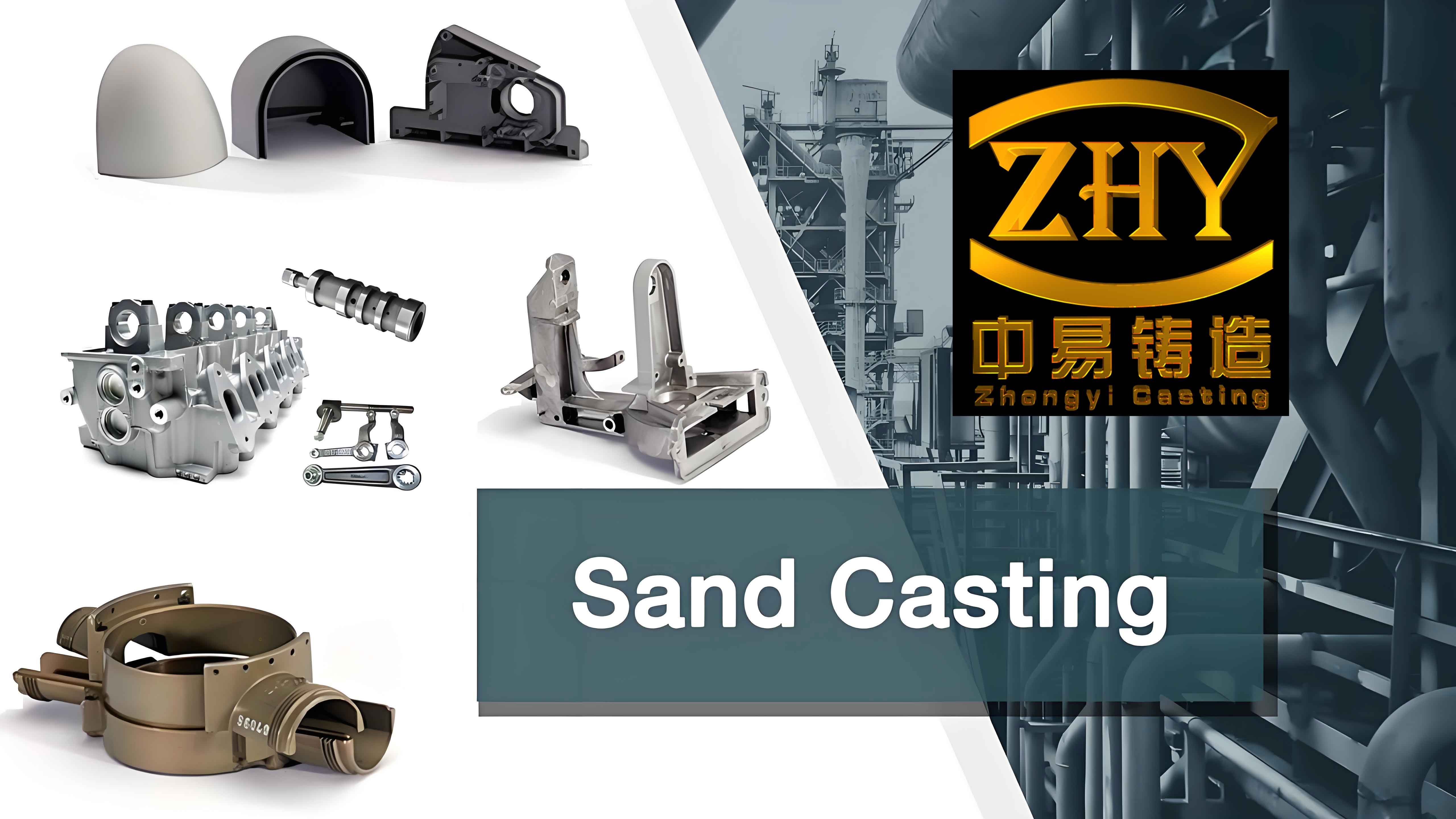
Importance of Surface Finishing for Sand Casting Parts
Surface finishing enhances the mechanical properties, aesthetic appeal, and durability of sand casting parts. It helps in removing surface imperfections, improving surface hardness, and increasing resistance to wear and corrosion. Proper surface finishing can significantly extend the lifespan of sand casting parts, making them more suitable for demanding applications.
Common Surface Finishing Methods
1. Machining
Machining involves removing material from the surface of sand casting parts using cutting tools. This method improves dimensional accuracy and surface finish.
- Applications: Engine components, machinery parts, industrial fittings
- Benefits: High precision, smooth surface finish, improved dimensional tolerance
2. Shot Blasting
Shot blasting uses abrasive materials, such as steel shots or grit, to clean and smooth the surface of sand casting parts.
- Applications: Structural components, automotive parts, aerospace components
- Benefits: Removes surface contaminants, enhances surface texture, improves surface hardness
3. Grinding
Grinding uses abrasive wheels to remove material and achieve a smooth surface finish on sand casting parts.
- Applications: Gear components, precision machinery parts, medical devices
- Benefits: High surface finish quality, precise control of surface geometry, removal of surface defects
4. Polishing
Polishing involves using fine abrasives to achieve a smooth and shiny surface on sand casting parts.
- Applications: Decorative components, precision instruments, optical parts
- Benefits: High aesthetic appeal, smooth and reflective surface, reduced surface roughness
5. Heat Treatment
Heat treatment involves heating and cooling sand casting parts to alter their microstructure and improve mechanical properties.
- Applications: High-stress components, automotive parts, industrial machinery
- Benefits: Improved hardness, increased strength, enhanced wear resistance
Table 1: Common Surface Finishing Methods and Their Benefits
Method | Applications | Benefits |
---|---|---|
Machining | Engine components, machinery parts | High precision, smooth surface finish, improved dimensional tolerance |
Shot Blasting | Structural components, automotive parts | Removes surface contaminants, enhances surface texture, improves surface hardness |
Grinding | Gear components, precision machinery parts | High surface finish quality, precise control of surface geometry, removal of surface defects |
Polishing | Decorative components, precision instruments | High aesthetic appeal, smooth and reflective surface, reduced surface roughness |
Heat Treatment | High-stress components, automotive parts | Improved hardness, increased strength, enhanced wear resistance |
Advanced Surface Finishing Techniques
1. Electropolishing
Electropolishing uses an electrochemical process to remove material from the surface of sand casting parts, resulting in a smooth and shiny finish.
- Applications: Medical devices, food processing equipment, aerospace components
- Benefits: Superior surface smoothness, enhanced corrosion resistance, reduced surface roughness
2. Plating
Plating involves depositing a thin layer of metal, such as nickel or chrome, onto the surface of sand casting parts.
- Applications: Automotive parts, electrical components, decorative items
- Benefits: Improved corrosion resistance, enhanced surface hardness, attractive finish
3. Anodizing
Anodizing is an electrochemical process that creates a protective oxide layer on the surface of aluminum sand casting parts.
- Applications: Aerospace components, consumer electronics, architectural fittings
- Benefits: Increased corrosion resistance, enhanced surface hardness, vibrant colors
4. Powder Coating
Powder coating involves applying a dry powder to the surface of sand casting parts, which is then cured under heat to form a protective layer.
- Applications: Outdoor furniture, automotive parts, industrial equipment
- Benefits: Durable finish, improved corrosion resistance, wide range of colors and textures
Table 2: Advanced Surface Finishing Techniques and Their Benefits
Technique | Applications | Benefits |
---|---|---|
Electropolishing | Medical devices, food processing equipment | Superior surface smoothness, enhanced corrosion resistance, reduced surface roughness |
Plating | Automotive parts, electrical components | Improved corrosion resistance, enhanced surface hardness, attractive finish |
Anodizing | Aerospace components, consumer electronics | Increased corrosion resistance, enhanced surface hardness, vibrant colors |
Powder Coating | Outdoor furniture, automotive parts | Durable finish, improved corrosion resistance, wide range of colors and textures |
Factors Influencing Surface Finishing Choice
Material of Sand Casting Parts
The material of the sand casting parts plays a significant role in determining the appropriate surface finishing method.
- Gray Cast Iron: Suitable for machining, grinding, and shot blasting
- Aluminum Alloys: Suitable for anodizing, polishing, and powder coating
- Steel Alloys: Suitable for plating, heat treatment, and grinding
Desired Surface Properties
The required surface properties, such as smoothness, hardness, and corrosion resistance, influence the choice of surface finishing technique.
- Smooth Surface: Polishing, electropolishing
- Hard Surface: Heat treatment, plating
- Corrosion-Resistant Surface: Anodizing, powder coating
Cost Considerations
The cost of surface finishing methods varies, and the choice depends on the budget and required quality of the final product.
- Low-Cost Methods: Shot blasting, machining
- High-Quality Methods: Electropolishing, plating, anodizing
List: Key Considerations for Surface Finishing
- Material of sand casting parts (gray cast iron, aluminum alloys, steel alloys)
- Desired surface properties (smoothness, hardness, corrosion resistance)
- Cost considerations (budget, quality requirements)
Conclusion
Surface finishing methods are essential for enhancing the durability and performance of sand casting parts. By selecting the appropriate finishing techniques, manufacturers can significantly improve the mechanical properties and aesthetic appeal of their products. Advances in surface finishing technology continue to provide innovative solutions for producing high-quality sand casting parts that meet the demanding requirements of various industries. As the demand for durable and high-performance components increases, the importance of effective surface finishing cannot be overstated.