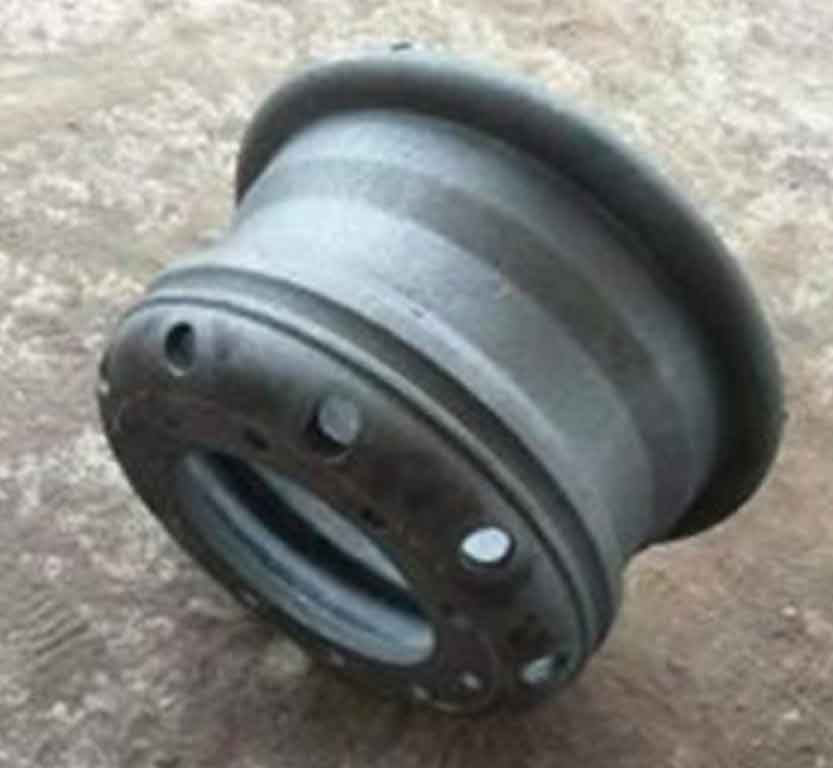
The most important characteristics of Vacuum casting is that molding sand is dry sand without binder.This method molds the sand with plastic film and makes mould hardening by evacuating the sand box.In virtue of the above characteristics which make modelling,sand shakeout, cleaning process simplified greatly, the supply equipment for edge mill and binder are no longer wanted, the shape and sand processing system can be simplified at the same time.
Vacuum casting, also known as vacuum-assisted casting or vacuum investment casting, is a specialized casting technique that involves the use of a vacuum to assist in the casting process. This method is often used in combination with investment casting (lost wax casting) to enhance the quality of castings and reduce defects. Here are the key characteristics and advantages of vacuum casting:
Characteristics:
- Reduced Porosity: One of the main benefits of vacuum casting is its ability to significantly reduce the formation of porosity and gas-related defects in the final casting. The vacuum helps to draw out and remove air and gases from the mold cavity and the molten metal, resulting in denser and more structurally sound castings.
- Improved Surface Finish: Vacuum casting can contribute to smoother and cleaner surface finishes on castings due to the reduced presence of entrapped air and impurities that can lead to surface defects.
- Better Metal Filling: The vacuum can aid in the complete and uniform filling of intricate details, undercuts, and thin sections of the mold, ensuring that the molten metal reaches all parts of the cavity.
- Enhanced Alloy Purity: By reducing gas-related defects and impurities, vacuum casting can help maintain the desired chemical composition and alloy purity of the final casting.
- Fine Detail Reproduction: Vacuum casting is particularly effective at reproducing intricate details and complex geometries, making it suitable for producing high-quality and highly detailed parts.
- Reduced Oxidation: The vacuum environment can help reduce the exposure of the molten metal to atmospheric oxygen, minimizing the risk of oxidation and surface defects caused by oxide formation.
Advantages:
- Improved Casting Quality: The primary advantage of vacuum casting is the improvement in casting quality, resulting in fewer defects, better surface finishes, and higher structural integrity of the final parts.
- Reduced Defects: Vacuum casting helps to minimize common defects such as porosity, shrinkage cavities, and gas-related defects, leading to more reliable and consistent castings.
- Enhanced Alloy Performance: For alloys that are sensitive to gas content or impurities, vacuum casting can ensure that the final castings meet the desired mechanical and metallurgical properties.
- Versatility of Materials: Vacuum casting can be used with a wide range of metals and alloys, including both ferrous and non-ferrous materials, allowing for versatility in casting applications.
- Precision and Detail: The combination of investment casting and vacuum-assisted technology allows for precise replication of intricate details and fine features, making it suitable for applications where high accuracy is required.
- Reduced Post-Casting Processing: With fewer defects and a smoother surface finish, castings produced through vacuum casting may require less post-casting finishing work, saving time and resources.
- Enhanced Melt Quality: The vacuum environment can contribute to the improved quality of the molten metal, reducing the likelihood of inclusions and other impurities.
Vacuum casting is commonly used in industries that require high-quality, precise, and defect-free castings, such as aerospace, medical equipment, and high-end jewelry production. It is particularly valuable when producing intricate components that demand both structural integrity and aesthetic appeal.
The advantages of Vacuum casting also make it wildly popular.Firstly,high accuracy of castings, clear outline, smooth surface have show perfect castings without flaws.Especially,when casting,the sand box keeps the vacuum state which is in favor of the liquid metal to fulfill the cavity.Secondly,Because cooling velocity of liquid metal is slow in the cavity, which is conducive to the supplement of metal, and increase the utilization ratio of metals, steel castings can be increased by 20%,iron castings can be increased by 25%.Thirdly,V casting can be used in iron casting, steel casting and other ferrous metals, and it can also be used for copper, aluminum and magnesium and other non-ferrous metal casting.So V casting can not only be applicable to the single and small batch production by hand,but also suitable for mechanical and automatic production.