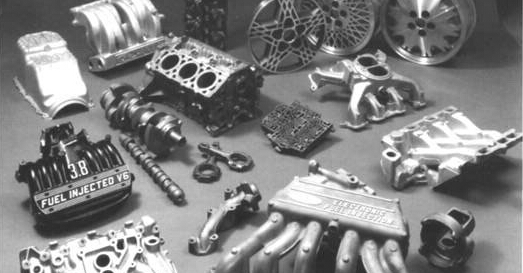
Chapter 1: The Introduction of Lost Wax Casting
Lost Wax casting is a kind of precision casting , is also called investment casting .
Lost Wax casting , in simple terms,that use fusible material ( such as wax and plastic ) for fusible mold , then , coating a number of layers special refractory coating on the mold , form integral shell through hardening , next , melt the mold , pouring liquid metal in it after roasting , casting will be got .
The alloy types that can be got by wax casting are : carbon steel , alloy steel , heat resisting alloy , stainless steel , precision alloy , permanent magnet alloy , bearing metal , copper alloy , aluminum alloy , titanium alloy and nodular iron casting , etc .
The shape of Lost wax casting usually is more complex , the hole minimum diameter is 0.5mm , the minimum wall thickness is 0.3mm . In production , some components that is made up by other several parts can directly be produced by wax casting through changing the structure of components . processing hour and metallic material can be saved and the structure of components will be more reasonable .
The weight range of wax casting mostly is from few grams to more than ten kilograms ( general not more than 25kg ) .
The process of wax casting is more complex and difficult to control , the material needed is more expensive , so ,it is applied to produce small parts that shape complex , high precision or difficult for other processing , like the blade of turbine engine .
Lost wax casting, also known as investment casting, is a traditional metal casting technique that dates back thousands of years. It involves the creation of intricate and detailed metal objects by utilizing a wax model that is “lost” or melted away during the casting process. This method allows for the production of highly detailed and complex shapes that might be difficult or impossible to achieve using other casting methods.
Here’s an overview of the steps involved in the lost wax casting process:
- Creating the Wax Model: The process begins with the creation of a wax model of the desired object. This can be done through various methods, including hand sculpting, 3D printing, or using molds. The wax model is an exact replica of the final metal object and includes all the intricate details.
- Assembly and Gating: Multiple wax models are often attached to a central wax rod called a “sprue.” The sprue acts as a channel through which molten metal will be poured into the mold. Additional wax rods, called “gates” and “risers,” are attached to the sprue to allow the molten metal to flow smoothly and to provide pathways for air and gases to escape during the casting process.
- Investment (Mold) Making: The assembly of wax models and sprue is then coated with a ceramic material, known as the investment. This investment is built up in layers to create a mold around the wax model. The investment mold is then heated to melt and remove the wax, leaving behind a hollow cavity in the shape of the original wax model.
- Preheating and Casting: The empty investment mold is preheated to a specific temperature to ensure that the molten metal will flow smoothly and evenly when poured into the mold. Once preheated, the mold is filled with molten metal using techniques like gravity pouring or vacuum-assisted casting. The metal fills the cavities left by the wax models, taking on their shape.
- Cooling and Solidification: After the mold is filled, the metal is allowed to cool and solidify within the mold cavity. The cooling process can take some time and is essential for achieving the desired metallurgical properties in the final casting.
- Mold Removal and Finishing: Once the metal has solidified and cooled, the investment mold is broken or dissolved away to reveal the cast metal object within. The sprue, gates, and risers are removed, and any remaining traces of the investment are cleaned off the metal surface. Depending on the desired finish, additional finishing processes like polishing, grinding, and machining might be carried out.
Lost wax casting is used to create a wide range of metal objects, including jewelry, sculptures, industrial components, and even dental prosthetics. It is valued for its ability to capture intricate details and produce high-quality, precise castings. While the basic principles of lost wax casting have remained consistent over time, modern technology and materials have enhanced the process, making it more efficient and adaptable to various applications.
Chapter 2: The Introduction of Lost Wax Casting
Here’s a detailed breakdown of the lost wax casting process:
- Pattern Creation: The process begins with the creation of a pattern, which can be made from wax, plastic, or other materials. This pattern represents the final metal object you want to create. Skilled artisans or modern technologies like 3D printing can be used to craft highly detailed patterns.
- Pattern Assembly: Multiple patterns are often attached to a central wax rod called a “sprue.” This assembly is called a “tree.” Additional wax rods, known as “gates” and “risers,” are attached to the sprue to facilitate the flow of molten metal and allow air to escape.
- Investment Mold Preparation: The tree of patterns is then coated with a refractory ceramic material known as the “investment.” The investment is applied in layers, and each layer is allowed to dry or harden. This buildup creates a mold around the patterns.
- Dewaxing (Burnout): Once the investment has dried, the entire mold assembly is heated in a kiln. The heat causes the wax patterns to melt and drip out, leaving behind cavities in the shape of the original patterns. This step is crucial to creating hollow castings.
- Preheating: After the wax has been removed, the mold is further heated to eliminate any residual moisture and ensure a smooth flow of molten metal. This also prevents thermal shock when the hot metal is poured into the mold.
- Casting: The preheated mold is placed in a casting furnace, and the desired metal, often in the form of ingots or grains, is melted in a separate crucible. The molten metal is then poured into the mold using gravity, vacuum, or pressure-assisted methods. The metal fills the cavities left by the wax patterns, creating a replica of the original object.
- Solidification: The filled mold is allowed to cool and the metal inside solidifies. The cooling process might take some time, and the speed at which it occurs can affect the metallurgical properties of the final casting.
- Mold Removal (Breakout): Once the metal has cooled and solidified, the investment mold is carefully broken or dissolved to reveal the cast metal object within. The sprue, gates, and risers are separated from the casting.
- Finishing: The casting is cleaned and any remaining traces of investment material are removed. Depending on the desired finish, additional processes like grinding, sanding, polishing, and even plating or enameling might be carried out.
- Quality Control: The finished casting is inspected for any defects, irregularities, or imperfections. Any necessary adjustments or corrections are made at this stage.
Lost wax casting is a versatile method used for creating a wide range of metal objects, from intricate jewelry pieces to complex industrial components. The level of detail and precision achievable with this method makes it a favored choice for producing high-quality metal castings.
Chapter 3: The Application of Iost Wax Casting
Lost wax casting, also known as investment casting, finds applications across various industries due to its ability to produce highly detailed and intricate metal objects. Here are some common areas where lost wax casting is applied:
- Jewelry: Lost wax casting is widely used in the jewelry industry to create intricate and finely detailed pieces. Jewelry designers can produce complex designs that might be challenging to achieve using other manufacturing methods. Rings, pendants, earrings, and other ornamental items are often created using this technique.
- Art and Sculpture: Artists and sculptors use lost wax casting to bring their creative visions to life. The process allows them to transform their intricate sculptures into metal artworks, preserving every delicate detail of the original sculpture.
- Dental Prosthetics: In dentistry, lost wax casting is used to create precise and customized dental prosthetics, such as crowns, bridges, and dentures. The process ensures that the prosthetics fit accurately and provide optimal comfort to the patients.
- Aerospace and Aviation: Lost wax casting is employed in the aerospace and aviation industries to create components for engines, turbines, and other critical parts. The precision and durability offered by this method make it suitable for producing high-performance components.
- Automotive Industry: The automotive sector uses lost wax casting to manufacture various engine and transmission components, as well as intricate decorative elements. The process helps achieve the desired strength and shape for these parts.
- Industrial Machinery: Lost wax casting is utilized to create parts for industrial machinery and equipment, such as pumps, valves, and gears. Complex geometries and tight tolerances can be achieved using this method.
- Medical Equipment: Medical instruments and equipment, including surgical tools and devices, can be produced using lost wax casting. The process ensures precision and quality for instruments that require delicate features.
- Agricultural and Farming Equipment: The agricultural sector benefits from lost wax casting for producing parts like gears, pulleys, and connectors for machinery and equipment used in farming.
- Artillery and Firearms: In the production of firearms and artillery, lost wax casting is used to create components like gun barrels, triggers, and firing mechanisms.
- Marine Industry: Components for boats, ships, and marine equipment can be fabricated using lost wax casting. This includes propellers, anchor parts, and marine fittings.
- Fashion Accessories: Beyond jewelry, lost wax casting can be employed to create high-end fashion accessories like belt buckles, cufflinks, and other intricate embellishments.
- Architectural Hardware: Lost wax casting is also used to create decorative architectural hardware such as doorknobs, handles, and hinges.
- Sculptural Restoration: This technique is utilized for restoring antique sculptures and artworks, ensuring that the original details are preserved during the replication process.
Lost wax casting’s versatility in producing complex shapes and intricate details makes it a favored method in various industries where precision and aesthetics are crucial. The advancement of technology, including computer-aided design (CAD) and additive manufacturing, has further expanded the applications and capabilities of this casting technique.
Chapter 4: The Advantage and Disadvantage of Lost Wax Casting
Lost wax casting, also known as investment casting, offers several advantages and disadvantages. Here’s a breakdown of the pros and cons of this casting method:
Advantages:
- Intricate Detail: Lost wax casting is renowned for its ability to reproduce intricate and complex details from the original pattern. This makes it suitable for producing highly detailed and ornate objects.
- Versatility: The process can be used with a wide range of metals, including precious metals like gold, silver, and platinum, as well as non-ferrous and ferrous alloys.
- Wide Range of Sizes: Lost wax casting can produce objects of various sizes, from tiny jewelry pieces to large industrial components.
- Smooth Finish: The casting process generally yields a smooth surface finish, reducing the need for extensive post-processing.
- Accuracy and Precision: The technique allows for tight tolerances and accurate reproduction of patterns, ensuring consistent and high-quality results.
- Complex Geometries: Lost wax casting can create parts with intricate shapes, undercuts, and irregular contours that might be difficult to achieve through other methods.
- Low Waste: The wax pattern is reusable, and excess material from gating and spruing can be recycled, making lost wax casting relatively efficient in terms of material usage.
- Design Freedom: Designers have more creative freedom in developing intricate and complex designs, as lost wax casting can capture even the smallest design elements.
Disadvantages:
- Time-Consuming: The lost wax casting process can be time-consuming due to the multiple steps involved, including pattern creation, mold making, casting, and finishing.
- Labor-Intensive: The process requires skilled artisans to create patterns, assemble trees, prepare molds, and carry out quality control. This can lead to higher labor costs.
- Initial Cost: The setup costs for lost wax casting, including equipment and materials, can be higher compared to other casting methods.
- Size Limitations: While lost wax casting can produce a wide range of sizes, very large castings might be challenging due to the limitations of the investment mold and the casting furnace.
- Mold Complexity: Creating and maintaining the investment mold can be intricate and requires careful attention to detail, which can lead to increased chances of defects if not executed correctly.
- Material Limitations: While lost wax casting can be used with a variety of metals, certain alloys or materials with high melting points may not be suitable due to the limitations of the investment materials.
- Porosity and Shrinkage: Porosity and shrinkage defects can occur during casting, affecting the mechanical properties of the final product if not properly controlled.
- Environmental Impact: The investment material and wax used in the process can generate waste and emissions during production, potentially impacting the environment.
In summary, lost wax casting offers exceptional detail, precision, and versatility, making it suitable for a wide range of applications. However, its disadvantages include the time, labor, and cost factors, as well as potential material limitations and environmental concerns. The decision to use lost wax casting should consider the specific requirements of the project and the desired balance between detail and production efficiency.