Chapter 1:Understanding Lost Foam Casting
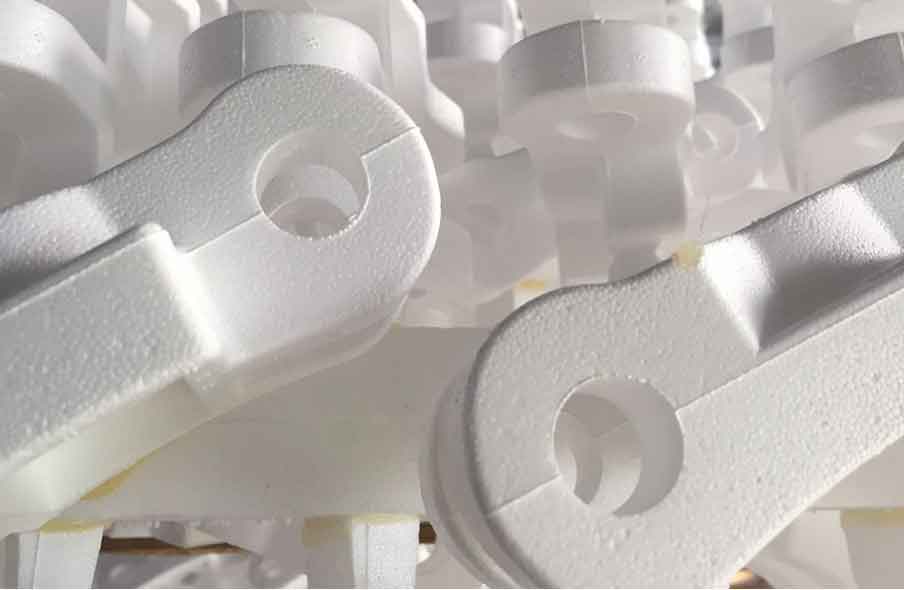
Lost foam casting is an innovative form of metal casting that has gained popularity in various industries due to its unique advantages. Here’s an overview of the process, its applications, and benefits:
Process
- Pattern Creation: The process begins with creating a foam pattern, which is a replica of the final casting. This pattern is typically made from polystyrene foam.
- Coating: The foam pattern is then coated with a refractory material, forming a thin shell around the foam. This shell will eventually determine the surface finish of the cast part.
- Assembly: These coated patterns are assembled onto a gating system made of the same foam material. This assembly is known as a cluster or tree.
- Molding: The coated patterns are then embedded into a flask filled with loose, unbonded sand, which is compacted around the foam pattern.
- Pouring: Molten metal is poured into the mold, replacing the foam pattern. The heat from the molten metal vaporizes the foam instantly, leaving the metal to fill the cavity in the shape of the pattern.
- Cooling and Cleanup: After the metal cools and solidifies, the sand is removed, revealing the cast metal part. The sand can be reclaimed and reused.
Applications
Lost foam casting is versatile and finds applications in a variety of industries:
- Automotive: Manufacturing engine parts, gears, and components with complex geometries.
- Aerospace: Production of lightweight, high-strength parts.
- Art and Sculpture: Creating intricate and detailed artistic pieces.
- Industrial Machinery: Producing large, complex machinery components.
Benefits
- Complex Geometries: Allows for the creation of parts with complex shapes and intricate details that would be difficult or impossible with traditional casting methods.
- Reduced Machining: Parts often require little to no machining after casting, as the process achieves close to net shape.
- Material Efficiency: Minimizes material waste, as the foam pattern is entirely consumed.
- High Dimensional Accuracy: Provides excellent dimensional accuracy and surface finish.
- Environmentally Friendly: The process generates less waste and can use recyclable materials, making it more environmentally friendly compared to some traditional casting methods.
Lost foam casting is a valuable process for producing complex shapes with high precision and minimal waste. Its versatility across various industries underscores its importance in modern manufacturing and engineering fields.
Chapter 2: Sustainable Approach to Complex lost foam casting Metal Parts Production
The sustainable approach to producing complex metal parts through lost foam casting involves several key considerations:
- Material Efficiency: Lost foam casting is known for its ability to produce complex shapes with minimal waste, as the foam pattern is vaporized and replaced by the metal. Selecting recyclable and reusable materials for both the foam and the casting metal can enhance sustainability.
- Energy Efficiency: Optimizing the energy use in the melting and casting process is crucial. This can be achieved by improving furnace efficiency, utilizing waste heat recovery systems, and adopting energy-efficient technologies.
- Emission Reduction: Managing emissions, particularly in the melting process, is important. This involves controlling the release of volatile organic compounds (VOCs) from the foam, and reducing greenhouse gases and particulate emissions from metal melting operations.
- Water Management: In many casting processes, significant amounts of water are used for cooling and other purposes. Implementing water recycling and treatment systems can minimize water waste and pollution.
- Waste Management and Recycling: Implementing strategies to recycle metal scraps and other materials used in the casting process, as well as proper disposal of non-recyclable waste, is important for minimizing environmental impact.
- Use of Safer Chemicals: Selecting foams and binders that are less harmful to the environment and to the health of workers can make the process more sustainable.
- Worker Safety and Health: Ensuring a safe working environment, particularly in terms of air quality and exposure to high temperatures and potentially harmful materials, is a critical aspect of sustainability.
- Lifecycle Analysis: Assessing the environmental impact of the entire lifecycle of the product, from material extraction through manufacturing, use, and end-of-life disposal or recycling, helps in making more informed, sustainable choices.
- Adoption of Renewable Energy Sources: Utilizing renewable energy sources, such as solar or wind power, for the energy-intensive parts of the process can significantly reduce the carbon footprint.
- Continuous Improvement and Innovation: Keeping up with technological advancements and continuously seeking ways to improve efficiency and reduce environmental impact is key for long-term sustainability in lost foam casting.
Implementing these practices can lead to a more sustainable approach in the production of complex metal parts, reducing environmental impact while maintaining or improving economic viability and product quality.
Chapter 3: The Role of Lost Foam Casting in Modern Manufacturing
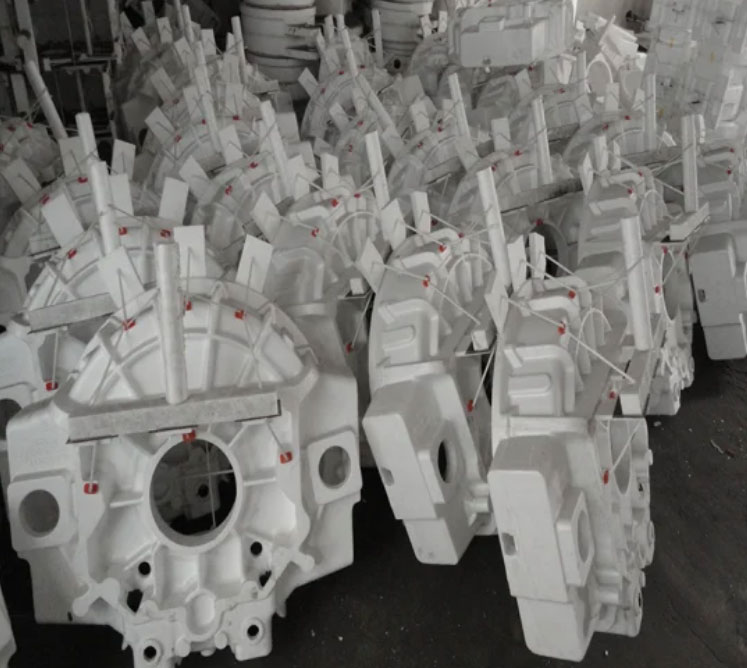
Lost foam casting plays a significant role in modern manufacturing, especially for producing complex metal parts. Here’s an overview of its importance:
- Complex Geometries and Precision: Lost foam casting allows for the creation of complex shapes with a high degree of precision. Since the foam model replicates the final product, manufacturers can produce intricate designs that might be challenging or impossible with traditional casting methods.
- Reduced Waste and Efficiency: This process can be more material-efficient than traditional casting methods. The foam pattern is consumed during the casting process, eliminating the need for mold extraction and reducing waste. This efficiency is particularly beneficial for expensive materials.
- Versatility in Materials: Lost foam casting is suitable for a wide range of metals and alloys. This versatility makes it an attractive option for industries requiring various materials, such as automotive, aerospace, and engineering.
- Cost-Effectiveness: For certain applications, lost foam casting can be more cost-effective than other casting methods, especially when producing complex shapes or a large volume of parts. The process reduces labor and machining costs and can lead to faster production times.
- Improved Surface Finish and Dimensional Accuracy: Parts produced through lost foam casting often have superior surface finishes and dimensional accuracy compared to those made with traditional sand casting. This reduces the need for additional machining and finishing processes.
- Customization and Flexibility: Lost foam casting is ideal for customized or short-run production. It allows for easy modification of designs and can be adapted quickly to changes in product requirements.
- Environmental Benefits: Lost foam casting can be more environmentally friendly compared to some traditional casting methods. The reduced waste and potentially lower energy consumption contribute to this aspect.
- Adaptability to Automation: The process lends itself well to automation, which can further enhance efficiency, reduce labor costs, and improve consistency in production quality.
Lost foam casting is an integral part of modern manufacturing due to its versatility, efficiency, and ability to produce complex, high-quality parts. It supports a range of industries, offering both economic and environmental advantages.
Chapter 4: Maximizing Efficiency with Lost Foam Casting
Maximizing efficiency in lost foam casting involves leveraging both existing best practices and ongoing innovations. This approach ensures the production of high-quality castings while minimizing waste and reducing costs. Here’s a look into how efficiency can be maximized in lost foam casting:
Insights for Maximizing Efficiency
- Pattern Material and Design:
- Use high-quality foam to ensure uniform density and minimize defects.
- Optimize pattern design to reduce material use and facilitate easy mold filling.
- Coating Optimization:
- Develop a consistent and appropriate coating thickness to ensure a good surface finish and prevent defects.
- Experiment with different refractory materials for the best results based on the metal being cast.
- Cluster Design:
- Design efficient gating and riser systems to ensure complete mold filling and proper feeding of the casting as it solidifies.
- Arrange patterns in a cluster to maximize the number of parts per casting cycle.
- Mold Compaction:
- Improve sand compaction around the foam pattern to ensure dimensional accuracy and minimize defects.
- Investigate alternative sand types or bonding methods for better mold stability and easier recovery.
- Melt Quality and Pouring:
- Ensure high-quality melt to reduce impurities and inclusions in the final casting.
- Control pouring temperature and rate to minimize turbulence and ensure smooth filling of the mold.
- Heat Management:
- Manage the heat during pouring effectively to ensure a steady vaporization of the foam and prevent mold defects.
- Automation:
- Incorporate automated processes for repetitive tasks to reduce labor costs and improve consistency.
Innovations in Lost Foam Casting
- Advanced Foam Materials:
- Research into new foam materials that can produce more accurate patterns and withstand the casting process better.
- 3D Printing of Foam Patterns:
- Utilize 3D printing to create complex foam patterns, allowing for more intricate designs and faster prototype development.
- Environmentally Friendly Coatings:
- Development of new, environmentally friendly coatings that are more effective and safer to use.
- Process Monitoring Technologies:
- Implement sensors and real-time monitoring systems to optimize the casting process, improve quality control, and reduce waste.
- AI and Machine Learning:
- Use AI algorithms to analyze data from the casting process, predict outcomes, and recommend adjustments for improved efficiency.
- Recycling and Material Recovery:
- Innovate in the recycling of waste materials, like sand and foam, to make the process more sustainable.
By combining these insights and innovations, manufacturers can significantly enhance the efficiency and effectiveness of the lost foam casting process. This not only leads to better-quality products but also contributes to cost reduction and sustainability in the manufacturing sector.
Chapter 5: The Versatility of Lost Foam Casting in Modern Industrial Applications
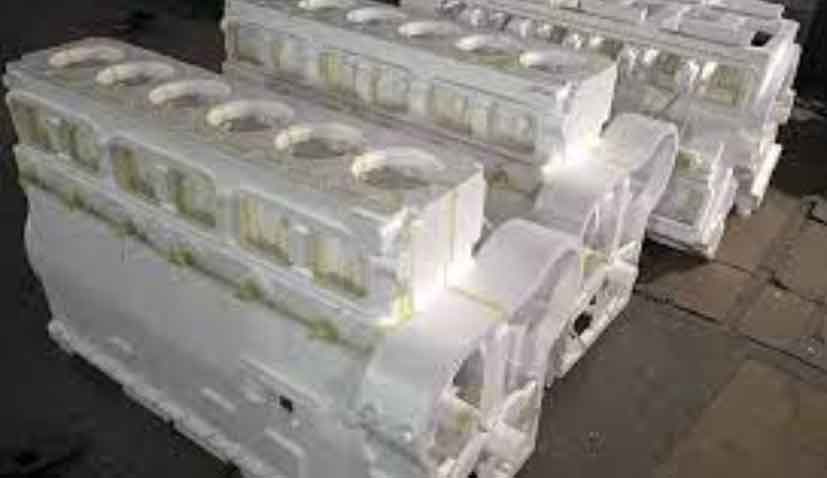
Lost foam casting, a type of evaporative-pattern casting, is a versatile and efficient manufacturing process widely used in modern industrial applications. Its uniqueness lies in the use of a foam pattern that evaporates upon contact with molten metal, providing several advantages:
- Complex Shapes and Sizes: This technique allows the creation of complex parts with intricate details that might be difficult or impossible to achieve with traditional casting methods. It’s particularly useful for parts with intricate internal passageways.
- Reduced Machining and Material Waste: Since the process can produce parts very close to their final shape, the need for machining is greatly reduced. This not only saves time but also reduces material waste, making it a more sustainable option.
- Versatile Material Options: Lost foam casting is compatible with a wide range of metals and alloys. This makes it a go-to choice for industries requiring various material properties, such as automotive, aerospace, and machinery manufacturing.
- Excellent Surface Finish and Accuracy: The technique typically results in a good surface finish and dimensional accuracy, reducing the need for further surface treatment.
- Cost-Effectiveness for Low to Medium Volume Production: While not always the most economical choice for high-volume production compared to processes like die casting, lost foam casting is cost-effective for low to medium volume productions due to its low tooling costs.
- Assembly Consolidation: Multiple parts can often be consolidated into a single casting, reducing the need for additional assembly and welding.
- Design Flexibility: Engineers and designers can experiment with complex and innovative designs without worrying about the limitations of traditional casting methods.
The lost foam casting process is particularly beneficial in sectors like the automotive industry (for engine components, housings, and manifolds), aerospace (for lightweight and strong parts), and industrial machinery (for complex, durable components). It represents a fusion of traditional craftsmanship and modern technology, offering a versatile solution for a wide range of industrial applications.
Chapter 6: The Role of Lost Foam Casting in Precision Manufacturing
Lost foam casting, also known as full mold casting, plays a significant role in precision manufacturing due to its unique advantages and applications. Here’s an overview of its role in this field:
- High Accuracy and Detail: Lost foam casting is renowned for its ability to produce parts with complex geometries and intricate details. This is because the foam pattern can be easily shaped into detailed designs, which are then accurately replicated in the final metal casting.
- Reduced Machining and Post-processing: Since lost foam casting can achieve close dimensional tolerances and excellent surface finishes, there is often a reduced need for extensive machining and post-processing. This saves time and resources in the manufacturing process.
- Versatility in Materials: This technique is compatible with a wide range of metals and alloys, making it a versatile choice for different industries. From aluminum and iron to high-nickel alloys, lost foam casting caters to various material requirements.
- Cost-Effective for Small to Medium Batches: While not as cost-effective as die casting for large production runs, lost foam casting is particularly advantageous for small to medium batch sizes. The process doesn’t require expensive mold materials, and the foam patterns are relatively inexpensive to produce.
- Environmentally Friendly: The process can be more environmentally friendly than traditional sand casting, as it generates less waste and harmful emissions. The expendable foam pattern vaporizes upon contact with the molten metal, leaving behind minimal residue.
- Applications Across Industries: Lost foam casting is used in a variety of industries, including automotive, aerospace, and medical equipment. Its ability to produce lightweight yet complex parts makes it ideal for manufacturing components like engine parts, gearboxes, and intricate medical devices.
- Integration with Modern Technologies: The process aligns well with modern manufacturing technologies. For instance, foam patterns can be created using CAD (Computer-Aided Design) and CNC (Computer Numerical Control) machines, enhancing precision and repeatability.
Lost foam casting is a valuable technique in precision manufacturing, offering high accuracy, versatility, and cost-effectiveness for specific applications and industries. Its compatibility with modern manufacturing technologies further enhances its role in producing high-quality, complex components.
Chapter 7: The Powerful Role of Lost Foam Casting in Production
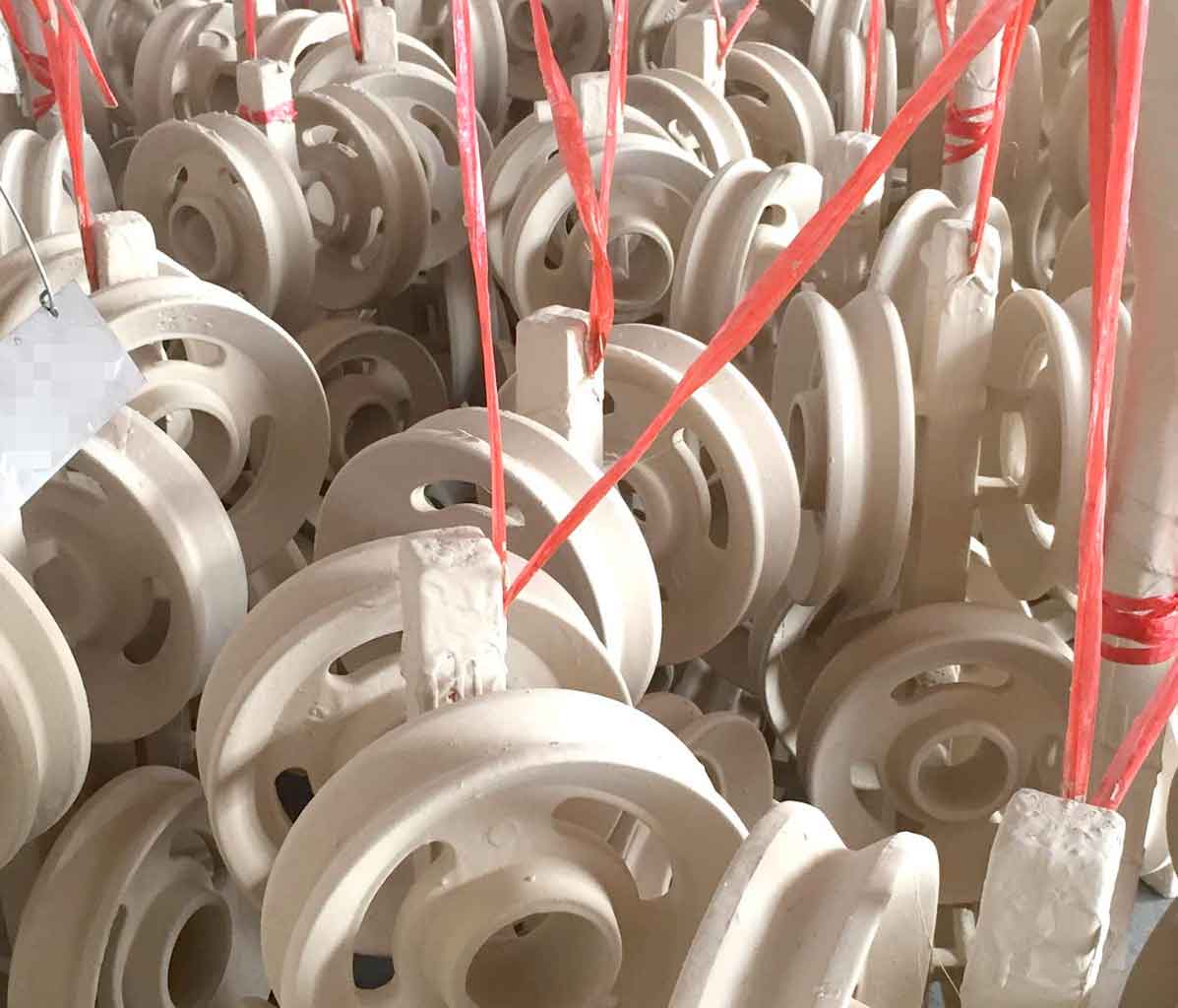
Lost foam casting is a type of evaporative-pattern casting process that is similar in nature to investment casting. This process is particularly significant in production due to several key aspects:
- Complex Geometries and High Precision: Lost foam casting allows for the production of complex shapes with a high level of precision and detail. This is because the foam pattern can be easily manipulated and it perfectly replicates the shape of the part to be cast. The accuracy and intricacy achievable with lost foam casting make it ideal for components that are difficult to shape using traditional casting methods.
- Reduced Machining and Post-processing: Since the casting can closely match the final shape of the component, there’s often a reduced need for extensive machining and finishing. This saves time and reduces the overall cost of production.
- Versatility in Materials: Lost foam casting can be used with various types of metals and alloys, enhancing its applicability across different industries, such as automotive, aerospace, and engineering.
- Improved Surface Finish and Dimensional Tolerances: The nature of the foam pattern and the mold material results in a smooth surface finish and tight dimensional tolerances, which are often a requisite in precision engineering.
- Cost-Effectiveness for Low to Medium Volume Production: For small to medium batch sizes, lost foam casting is particularly cost-effective. It doesn’t require expensive tooling like some other casting methods, making it more feasible for limited runs.
- Environmentally Friendly Process: The method can be considered more environmentally friendly compared to traditional sand casting. It generates less waste and the foam used is often recyclable, reducing the environmental footprint.
- Flexibility in Design Changes: If a design change is necessary, it is generally easier and cheaper to modify or replace foam patterns compared to altering permanent molds used in other casting processes.
- Consistency in Production: Lost foam casting offers consistent quality in the production of parts, as the process is largely controlled and repeatable.
- Minimized Assembly Operations: By allowing the integration of multiple parts into a single casting, lost foam casting reduces the need for extensive assembly operations. This integration can lead to stronger, more reliable parts with fewer points of potential failure.
Lost foam casting is a powerful method in the manufacturing world, particularly beneficial for complex, precise components where quality, cost, and flexibility are critical considerations. Its advantages have made it a preferred choice in industries like automotive, aerospace, and heavy equipment manufacturing.
Chapter 8: Techniques and Best Practices in Lost Foam Casting
Lost Foam Casting is an advanced casting process that offers several advantages over traditional casting methods, including greater design freedom, higher dimensional accuracy, and smoother surface finishes. Here are some techniques and best practices for successful Lost Foam Casting:
- Pattern Creation: In lost foam casting, the pattern is made from polystyrene foam, which is easy to shape and carve. It’s important to ensure the pattern’s dimensional accuracy, as the final casting will replicate its shape. The foam pattern is typically coated with a refractory material to improve surface finish and dimensional accuracy.
- Cluster Assembly: Multiple foam patterns can be glued together into a cluster to be cast simultaneously. This assembly must be carefully done to ensure proper flow of molten metal and to avoid defects.
- Mold Filling: A key aspect of lost foam casting is the mold filling process. The mold is filled with dry, unbonded sand which is compacted around the foam pattern. There’s no need for binders or a separate molding box, reducing the complexity of the process.
- Pouring Technique: The pouring technique in lost foam casting is crucial. Molten metal is poured directly into the foam-filled mold, which vaporizes the foam upon contact. The flow rate and temperature of the molten metal are critical factors. A controlled pouring rate minimizes turbulence and ensures a defect-free casting.
- Cooling and Solidification: After pouring, the metal needs time to cool and solidify. The cooling rate can affect the microstructure and mechanical properties of the casting. It’s important to control the cooling rate to achieve the desired properties.
- Sand Removal and Cleaning: After the metal has solidified, the sand is removed from the casting. This process often involves vibration or air blasting. Finally, the casting is cleaned to remove any remaining sand or surface imperfections.
- Quality Control: Continuous quality control is vital. Inspecting the foam patterns, monitoring the pouring process, and conducting post-casting inspections are all essential to ensure high-quality castings.
- Environmental Considerations: Lost foam casting is more environmentally friendly than traditional sand casting methods, as it produces less waste and uses fewer harmful chemicals. However, managing the waste foam and emissions is still important.
By following these techniques and best practices, manufacturers can leverage the benefits of Lost Foam Casting to produce complex, high-quality castings with minimal waste and high efficiency.
Chapter 9: The Comprehensive Guide to Lost Foam Casting Techniques and Applications
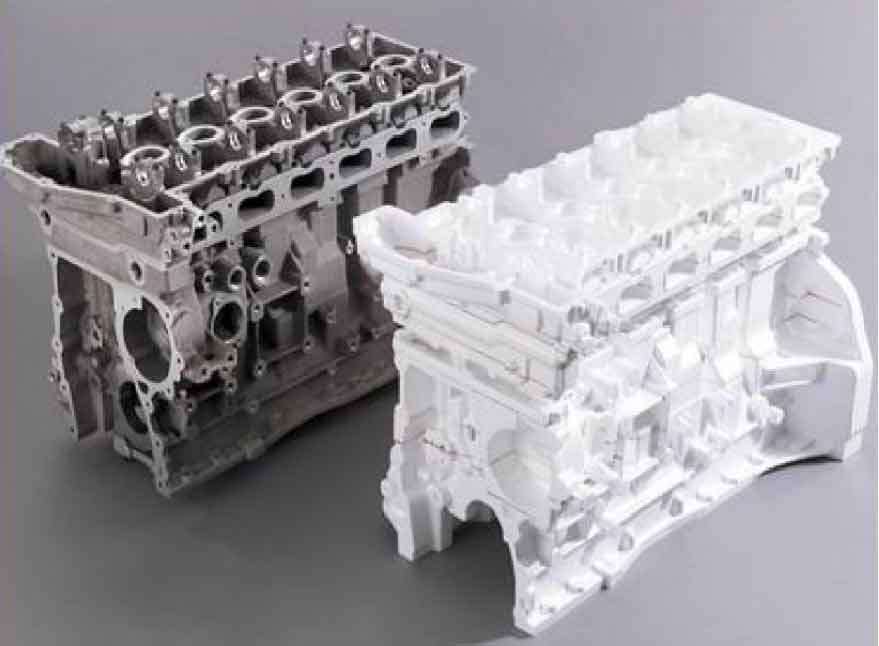
Lost Foam Casting is a type of evaporative-pattern casting process that is similar to investment casting except foam is used for the pattern instead of wax. This process is beneficial for casting metals with complex geometries and intricate details. Here’s a comprehensive guide to the techniques and applications of Lost Foam Casting:
1. Overview of Lost Foam Casting
- Definition: Utilizes a foam pattern that evaporates upon contact with molten metal to create complex metal parts.
- History and Development: Evolved from full mold process developed in the 1950s.
2. Materials Used
- Foam Types: Usually polystyrene or polyurethane foams.
- Metal Types: Suitable for various metals including aluminum, iron, steel, and non-ferrous alloys.
3. Pattern Creation and Assembly
- Designing the Pattern: CAD and other design tools are employed.
- Creating Foam Patterns: Techniques like molding or machining.
- Assembling Patterns: Gluing smaller foam pieces to create the final pattern.
4. Casting Process
- Coating the Foam Pattern: With refractory material for smooth surface finish.
- Creating the Mold: The coated pattern is embedded in sand without binders.
- Pouring the Metal: Molten metal is poured, evaporating the foam and filling the cavity.
- Cooling and Solidification: Metal cools and solidifies in the shape of the pattern.
5. Post-Casting Processes
- Removal of Residuals: Cleaning off sand and other residues.
- Finishing Techniques: Like grinding, polishing to achieve the desired surface quality.
6. Advantages and Limitations
- Advantages: Ability to cast complex geometries, reduced waste, and minimal machining.
- Limitations: Pattern collapse issues, porosity in final product, limited pattern material choice.
7. Applications
- Automotive Industry: Engine parts, chassis components.
- Aerospace Sector: Lightweight structures.
- Art and Sculptures: Complex shapes and designs.
- Engineering and Manufacturing: Custom machinery parts.
8. Future Developments and Innovations
- Integration with 3D printing for pattern making.
- Development in foam materials for higher precision.
9. Health, Safety, and Environmental Considerations
- Handling and disposal of evaporated foam products.
- Safety measures during the casting process.
10. Case Studies and Real-World Examples
- Analysis of specific industries where lost foam casting has significantly impacted production and design.
11. Comparative Analysis with Other Casting Methods
- Comparison with traditional sand casting, investment casting, etc., in terms of cost, complexity, and quality.
12. Training and Skill Development
- Required skills for technicians and engineers.
- Training programs and certifications.
13. Economic Aspects
- Cost analysis and return on investment for adopting lost foam casting in manufacturing.
14. Quality Control and Testing
- Methods for ensuring the quality of cast products.
- Standard testing procedures.
Conclusion
Lost Foam Casting is a versatile and efficient method for producing complex metal parts, offering advantages in design flexibility and cost-effectiveness. It continues to evolve with advancements in materials and technology, broadening its applications in various industries.
This guide provides a detailed understanding of lost foam casting techniques and applications, and it’s essential for professionals and enthusiasts in the fields of metallurgy, manufacturing, and engineering.
Chapter 10: Achieving Precision and Efficiency with Lost Foam Casting in Aerospace and Automotive Industries
Achieving precision and efficiency in Lost Foam Casting is particularly crucial in sectors like aerospace and automotive industries, where the quality and accuracy of components are paramount. The integration of lost foam casting in these industries has led to significant advancements. Here’s how precision and efficiency are achieved with lost foam casting in these sectors:
Aerospace Industry
- Complex Geometry and Lightweight Requirements:
- Lost foam casting allows for the creation of complex, lightweight components essential for aerospace applications.
- The process minimizes material wastage, crucial for expensive aerospace alloys.
- High Precision Manufacturing:
- Lost foam casting offers high dimensional accuracy, essential for aerospace components where tolerances are tight.
- The foam patterns can be precisely machined or 3D printed, ensuring exact replicas of the desired part.
- Material Variety:
- The ability to cast different alloys, including high-performance materials suitable for aerospace applications, is a key advantage.
- Cost-Efficiency in Low to Medium Volume Production:
- Lost foam casting is cost-effective for producing small to medium batches of parts, typical in aerospace manufacturing, due to lower tooling costs compared to other casting methods.
Automotive Industry
- Mass Production and Consistency:
- The automotive industry benefits from lost foam casting’s ability to consistently produce large volumes of parts with uniform quality.
- Automation in the lost foam casting process further enhances efficiency and consistency.
- Reduced Machining and Finishing:
- Lost foam casting’s accuracy reduces the need for extensive machining and finishing, thus saving time and reducing costs.
- The surface finish achieved with lost foam casting is generally superior to other casting methods, an important factor in automotive parts.
- Design Flexibility:
- The flexibility in designing foam patterns allows for the integration of intricate designs and undercuts, enabling more innovative automotive components.
- It facilitates integration of multiple parts into a single casting, reducing assembly requirements.
- Weight Reduction for Fuel Efficiency:
- The ability to produce complex, lightweight components contributes to overall vehicle weight reduction, enhancing fuel efficiency – a critical aspect in modern automotive design.
Common Advancements and Challenges in Both Industries
- Integration of Advanced Technologies:
- The use of CAD, CAM, and 3D printing for creating precise foam patterns.
- Advanced simulation software for predicting and enhancing casting outcomes.
- Quality Control and Testing:
- Rigorous testing protocols to ensure that the components meet industry-specific standards.
- Non-destructive testing methods like X-ray and ultrasound are frequently used.
- Environmental and Safety Considerations:
- Managing waste and emissions, especially concerning the evaporation of foam materials.
- Ensuring safe handling of molten metals and chemicals used in the process.
- Challenges:
- Managing the porosity and integrity of cast parts remains a challenge.
- Ensuring the stability of foam patterns during casting is crucial for quality.
Conclusion
In conclusion, Lost Foam Casting has become a pivotal technology in the aerospace and automotive industries due to its ability to produce complex, high-quality parts efficiently and cost-effectively. As these industries continue to evolve towards more advanced and lightweight designs, Lost foam casting’s role is to expand, driven by ongoing innovations in materials, design methodologies, and production technologies.