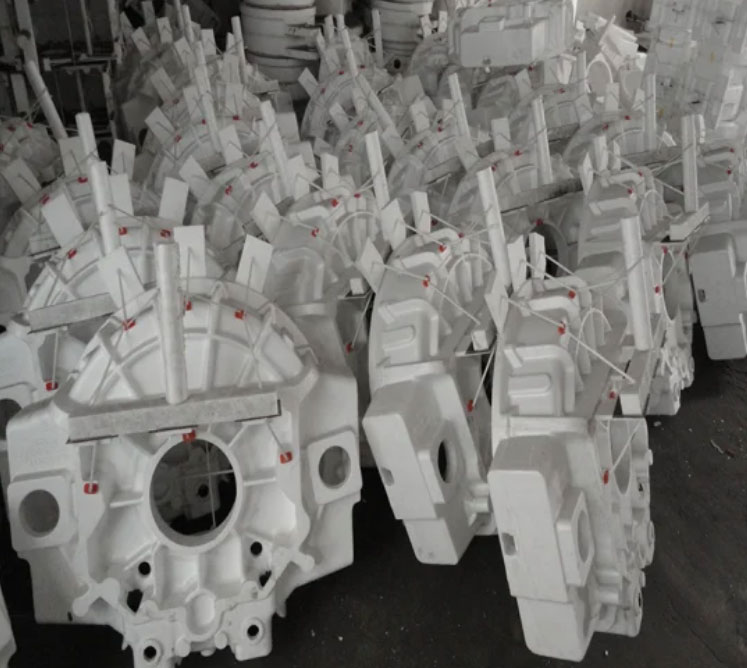
Lost foam casting (LFC) is a versatile casting process that offers designers and engineers unprecedented design freedom to create complex and intricate metal parts. The unique capabilities of lost foam casting enable the unleashing of creativity in various ways:
1. Complex Geometries:
Lost foam casting allows for the production of parts with intricate and complex geometries that may be difficult or impossible to achieve using other casting methods. The foam patterns used in LFC can be easily shaped to match the desired part geometry, enabling the creation of parts with challenging shapes, undercuts, and thin sections.
2. Intricate Details:
The foam patterns used in lost foam casting can be accurately detailed, capturing fine features and intricate designs. This includes the reproduction of intricate patterns, textures, and surface details that are essential in artistic and decorative components.
3. Single-Piece Designs:
Lost foam casting enables the creation of single-piece designs, eliminating the need for complex assembly or welding of multiple parts. This not only streamlines the production process but also ensures better part integrity and reduced post-processing requirements.
4. Hollow Sections and Internal Passages:
Lost foam casting allows the creation of hollow sections and internal passages within a part, which can be advantageous for reducing weight and enhancing functionality. The foam patterns can be easily designed with cavities and cores to produce parts with complex internal structures.
5. Freedom from Tooling Constraints:
Traditional casting methods often require expensive and time-consuming tooling, limiting design iterations and modifications. In lost foam casting, the foam patterns are relatively easy and cost-effective to produce, allowing designers greater flexibility in design changes and iterations.
6. Lightweight and Complex Shapes:
The design freedom in lost foam casting facilitates the production of lightweight components with complex shapes. This is particularly advantageous in industries like aerospace and automotive, where weight reduction and aerodynamic efficiency are critical.
7. Customization and Prototyping:
Lost foam casting is ideal for rapid prototyping and small-scale production of custom parts. Designers can quickly create and modify foam patterns to test and validate new designs, making the process highly suitable for custom or one-off creations.
8. Artistic and Sculptural Applications:
Lost foam casting is widely used in artistic and sculptural applications due to its ability to reproduce intricate artistic designs and detailed sculptures. It allows artists and sculptors to transform their creative visions into solid metal forms with minimal constraints.
9. Complex Casting Combinations:
Lost foam casting can be combined with other casting techniques, such as sand casting or investment casting, to produce even more complex parts or components with specific material requirements.
Lost foam casting provides designers with the freedom to push the boundaries of conventional design constraints, enabling the realization of innovative and artistic creations as well as highly functional and efficient engineering components. Its ability to capture the most intricate details and achieve complex geometries makes it a preferred choice for a wide range of industries seeking design versatility and flexibility.