The lost foam casting process is developed from the full mold casting process,In 1981, the Chinese Academy of Sciences developed China’s first lost foam castingFor more than 40 years, the production line has benefited from its technological advantages,Casting has been improved in terms of technology, equipment, mold design, raw materials, etc.The engineering design of lost foam casting plants is also constantly optimizedto adapt to the development of environmental protection, safety, green and energy conservation in ChinaIdeas.
1 Features of lost foam casting process
The lost foam casting is a process of using wax with similar size and shape to the castingOr bond the foamed resin model to form a model cluster, and brush with refractory paintAfter painting and drying, it is vibrated and molded in dry quartz sand under negative pressure.Lower the pouring, vaporize the model, and the liquid metal occupies the model position and solidifiesA new casting method that forms a casting after cooling.Compared with the common sand casting process in the foundry industry, the lost foam casting processThe characteristics of casting technology are:1) Use the combination of foam plastics to producecastings, allowing for more freedom in designing the structure of castings and producing complex shapesProduct.It is particularly suitable for the production of multi-edge, multi-core, complex geometric shapes that are difficult to mold. Currently, it is the main casting method for the production of motor housing castings.The manufacturing process.2) The green sand casting process generally requires sand for complex castings.Core, sand core preparation process often produces harmful smoke.Among them, cold coreThe treatment technology of triethylamine tail gas generated by the core making process is becoming more and more mature, which canThe smoke, organic waste gas and odor generated by the hot core should be effectively controlled.The technical difficulty of thorough treatment is very high and the cost is very high.However, the lost foam castingThe casting process does not require sand cores and is a clean and environmentally friendly casting process.3) There is no chemical binder in the lost foam casting sand, and the old sand is recycledThe rate is high, usually reaching more than 90%, which is in line with the current strict environmental protection requirements.The energy consumption cost savings rate of casting production is around 15%,The cost of parts is reduced by about 30%.4) The castings produced by the lost foam casting process have no flash, burr, andDraft angle, high dimensional accuracy of castings, less reserved machining volume, cleaningThe grinding workload is reduced by more than 50%, and the surface quality of the casting is good.Generally speaking, investment in lost foam casting equipment is lower than that in sand casting equipment.The investment casting can reduce 30% to 50%.According to the characteristics of the lost foam casting process, its production area mainlyIt is divided into white zone, gray zone and black zone.The process flow of lost foam casting is shown in Figure 1as shown.
The white zone and grey zone of the lost foam workshop are usually set in one place, calledIt is a mold workshop, a unique workshop for the lost foam casting process, which is mainly used to produce qualified mold bundles.It includes bead pre-foaming, pre-extrusion,Curing after foaming, mold piece making, mold piece aging, gluing, coating and bakingDry waiting process.There are many forms of pre-foaming, such as hot water pre-foaming, steamPre-foaming and vacuum pre-foaming, commonly used in the form of steam pre-foaming.When making the mold piece, steam is introduced into the mold to heat the beads so that the foam is heatedSoftening, swelling, filling all gaps between beads in the mold cavity, and adhesioninto a whole.The black area of the lost foam workshop is similar to the sand mold workshop, including the melting workers.The department, the molding department, the sand processing department, and the cleaning department are commonly referred to as the elimination department.The lost-form workshop.The characteristic of lost foam molding is to fill the sand box with dry sand and use vacuumThe negative pressure is pumped into a solid mold.The molding process is:Add bottom sand and vibrate→install formwork bundle → shape and vibrate on the vibrating table with sandSolid→coating and sanding → adding a pouring cup→pouring→cooling→turningBox→sand falling conveyor → vibrating conveyor chute→casting.The sand used for sand processing is dry sand without any additives, and the equipment is simple.The process of dry sand treatment is as follows:Hydraulic turnover machine→vibration conveyor sand dropping chute → high temperature resistant bucket elevatorMachine→vibration sand screening machine → magnetic separator→automatic sand feeding door→air coolingBed→bucket elevator → intermediate sand storage (upper and lower level gauges)→bucket elevator→Sand temperature regulator → automatic sand feeding door→bucket elevator→molding sand silo.The lost foam workshop has no core making department, melting department and cleaning departmentSimilar to common sand molding workshop.
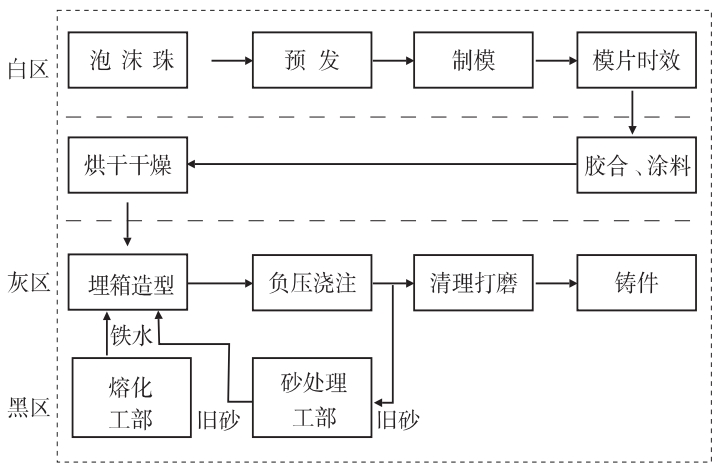
2 Key points of engineering design for lost foam casting
The lost foam casting process uses a large amount of resin raw materials, which can cause fires.The fire safety design is related to whether the project can be smoothly implemented by the government.Acceptance is an important factor that must be considered in design.Among them, mold makingThe fire hazard rating between the two workshops is higher than that of the lost foam workshop.The requirements for fire protection design vary greatly, and the investment is also very different.Based on thisIn the engineering design of new lost foam casting plants, it is preferred toThe molding workshop and the lost foam workshop are set as independent building sub-items to reduce the fire protection design cost of the lost foam workshop.
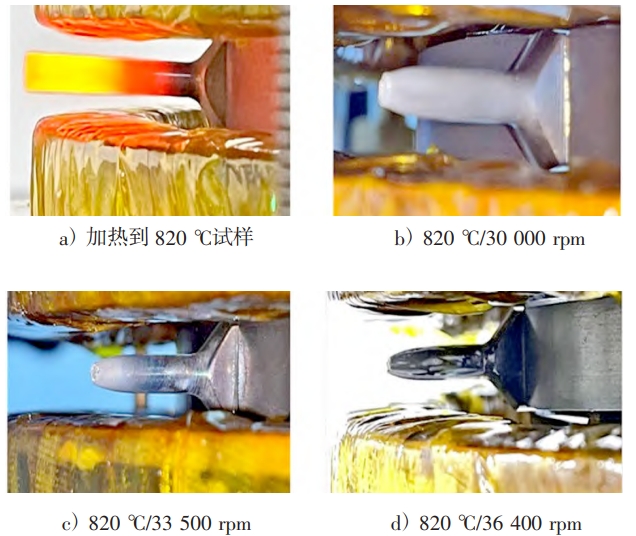
3 Conclusion
1) Developed a high-speed rotating blade that meets the requirements of in-situ heating on the experimental benchThe induction coil required has a rated heating temperature of 1050℃.2) The test results of the heating temperature field of the sample show that at current,Under the condition of constant power and frequency, the induction coil can beA stable temperature load was applied to the sample, which verified the development ofThe induction coil of has good performance both in static and dynamic state.Heating performance, stable location of temperature equalization zone, temperature and setting of temperature equalization zoneThe temperature deviation shall not exceed 10℃.3) Through three sets of creep experiments under high temperature and high speed,Verified that the induction coil developed can work with the high-speed rotating test bench,Prepare to carry out long-term high temperature-high speed coupling effects on materials or componentsThe ability to test and solve the current lack of conventional material performance testing equipmentThe key to testing material properties under high temperature-high speed coupling conditionsDifficult problem.
With the development of lost foam casting technology becoming more and more mature,The mold casting workshop has the characteristics of low investment and strong product adaptability.There are more and more projects of lost foam casting, aiming at lost foam casting engineeringThe requirements for design are becoming higher and higher.In the design of lost foam casting engineering,Pay attention to the following points: 1) The mold workshop should pay special attention to its fire hazard.The impact of grades on engineering design and project cost.In the engineering designAt the beginning, it is possible to communicate well with the local fire control department to facilitate the completion of fire safety acceptance inspection and other work for the project as soon as possible in the later stage;2) mold bundle pouringNote: It should be carried out under negative pressure conditions, and a vacuum pump room should be established and reasonably set up.set up a vacuum point;3) the sand processing department should set up cooling equipment nearby to improve the work efficiency.For circulating cooling water to effectively cool the high temperature sand.Currently in the mold workshopThe automation level of the two projects is relatively low, and the engineering design in the future needs to focus onHow to improve the automation level of the mold workshop.