There are many kinds of cast iron parts for engine block. The main classification methods are the number of cylinders and the arrangement of cylinders.
According to the number of cylinders, there are mainly single cylinder and multi cylinder engine block. Four cylinder, six cylinder, eight cylinder and sixteen cylinder are widely used in automobile, engineering machinery, ship and other fields. The cast iron castings of cylinder block are four to sixteen cylinders, as shown in Figure 1.
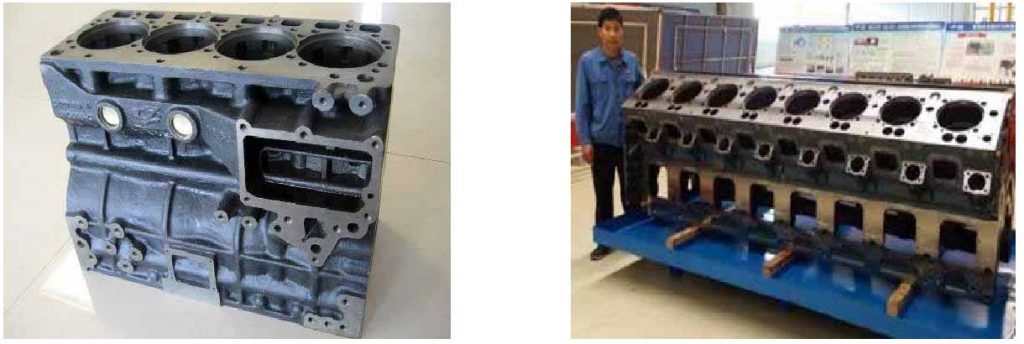
According to the cylinder arrangement, there are mainly in-line (L-type), V-type, W-type (V-type engine variant) and horizontal opposed type. The cast iron castings of cylinder block are L-type and V-type, as shown in Fig. 2.
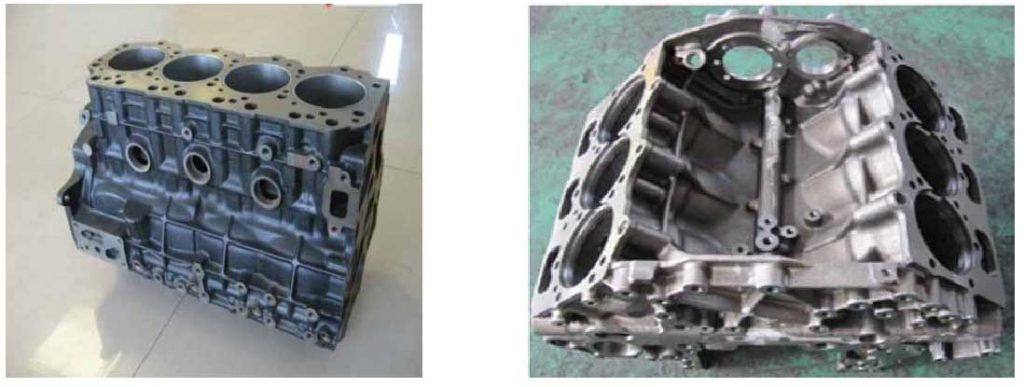
The classification of cast engine blocks primarily revolves around the type of material used in their construction and the specific casting techniques employed. These factors significantly influence the engine block’s properties, including its strength, weight, thermal conductivity, and overall performance. Here’s a closer look at the common classifications:
Based on Material
- Grey Cast Iron Engine Blocks
- Made from grey cast iron, characterized by its graphite flake microstructure.
- Offers excellent thermal conductivity, good machinability, and vibration damping properties.
- Commonly used due to its cost-effectiveness and sufficient strength for a wide range of automotive applications.
- Ductile Cast Iron Engine Blocks
- Constructed from ductile cast iron (also known as nodular cast iron), which contains spherical graphite nodules.
- Provides greater strength and ductility compared to grey cast iron, allowing for thinner wall constructions and potentially lighter engine blocks.
- Used in more demanding applications where additional strength is required without a significant weight penalty.
- Compacted Graphite Iron (CGI) Engine Blocks
- Made from compacted graphite iron, which features a graphite structure that is somewhere between the flake graphite of grey cast iron and the spherical graphite of ductile cast iron.
- Offers better strength and thermal characteristics than grey cast iron, with better castability and machinability than ductile cast iron.
- Increasingly popular for high-performance and diesel engines where higher strength and temperature resistance are needed.
Based on Casting Technique
- Sand Casting
- The traditional casting method where molten metal is poured into a sand mold.
- Suitable for both small and large volume productions.
- Sand casting is versatile and can be used for casting both grey and ductile cast iron engine blocks. It’s widely used because of its simplicity and adaptability to different engine block designs and sizes.
- Die Casting
- A method where molten metal is forced into a metal mold under high pressure.
- Not typically used for cast iron engine blocks due to the material properties and the high temperatures involved, but more common for aluminum engine blocks.
- Offers a high degree of dimensional accuracy and smoother surface finishes.
- Permanent Mold Casting
- Similar to die casting but uses a reusable mold.
- This method is less common for cast iron engine blocks due to the material’s characteristics but is another method used for aluminum blocks.
- It provides a good surface finish and dimensional consistency.
- Shell Molding
- A casting process that uses a resin-covered sand to form a shell-like mold.
- Offers better surface quality and more precise dimensions than traditional sand casting.
- This method can be used for complex shapes and is suitable for casting high-grade grey and ductile cast iron engine blocks.
The choice of material and casting technique for an engine block largely depends on the engine’s specific performance requirements, production volumes, and cost constraints. Grey cast iron remains the staple for most standard automotive applications due to its balance of performance, machinability, and cost. In contrast, ductile cast iron and CGI are selected for applications requiring higher strength and lighter weight, albeit at a higher cost. The casting technique is chosen based on the desired production volume, complexity of the engine block design, and the required material properties.