Custom sand casting parts provide tailored solutions to meet specific industry needs. With sand casting, manufacturers can produce highly customizable and intricate parts that align with unique design requirements. Here are some key aspects of custom sand casting parts:
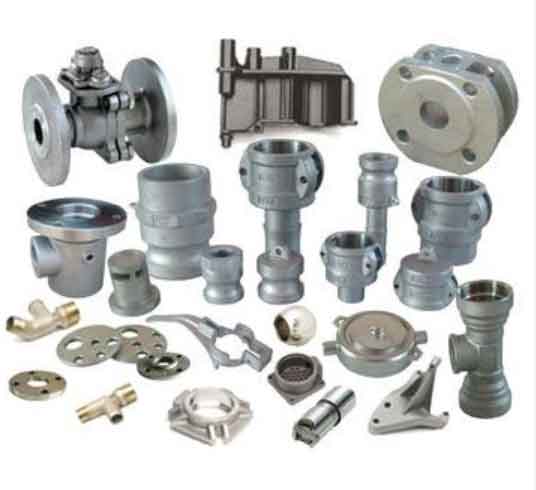
- Design flexibility: Sand casting allows for the production of complex and intricate part geometries, including thin walls, undercuts, and internal features. This design flexibility enables manufacturers to create custom parts that meet specific functionality and performance requirements.
- Material selection: Sand casting accommodates a wide range of materials, including various alloys of aluminum, iron, steel, and more. The choice of material can be tailored to the specific needs of the industry, such as strength, corrosion resistance, heat resistance, or wear resistance.
- Size and weight range: Sand casting can produce parts of varying sizes and weights, from small components to large and heavy structures. This versatility makes it suitable for industries with diverse requirements, such as automotive, aerospace, construction, and energy.
- Prototyping and low-volume production: Custom sand casting is well-suited for prototyping and low-volume production. It allows manufacturers to quickly produce prototype parts for testing and validation before scaling up to higher volumes if needed.
- Cost-effectiveness: Sand casting can be a cost-effective option for custom part production, especially for larger components or low-volume production runs. The relatively low tooling costs and flexibility in material selection contribute to its cost advantages.
- Part consolidation: Sand casting enables the integration of multiple components into a single complex casting. This eliminates the need for separate machining, welding, or assembly operations, reducing overall production time and cost.
- Industry-specific applications: Custom sand casting parts find applications across various industries. For example, in the automotive industry, custom sand castings are used for engine components, transmission housings, and suspension parts. In the energy sector, they are utilized for turbine components, pump casings, and valves. In construction, custom sand castings are employed for structural components and architectural elements.
- Collaborative design process: Custom sand casting parts often involve close collaboration between the manufacturer and the customer. Manufacturers work closely with clients to understand their specific needs, provide design assistance, and optimize the part design for sand casting.
By leveraging the capabilities of custom sand casting, industries can obtain precisely tailored solutions that meet their unique requirements. The ability to produce complex geometries, choose suitable materials, and accommodate various sizes and weights make custom sand casting an ideal choice for industries seeking highly customized and efficient part solutions.