Lost foam casting technology is made of polystyrene foam through the foaming process and the shape of the needed castings. It is used as a mold for molding. After filling the sand, the foam pattern does not take out the mold, and then pouring the metal into the mold to vaporize the mould to form the casting. Lost foam casting molding technology adopts dry sand for molding, which does not need the binder used in wet sand mold and resin sand mold and additives such as pulverized coal, bentonite and water. It has less demand for raw materials, saves raw materials, and the old sand can be recycled after simple treatment, so as to reduce the pollution to the environment.
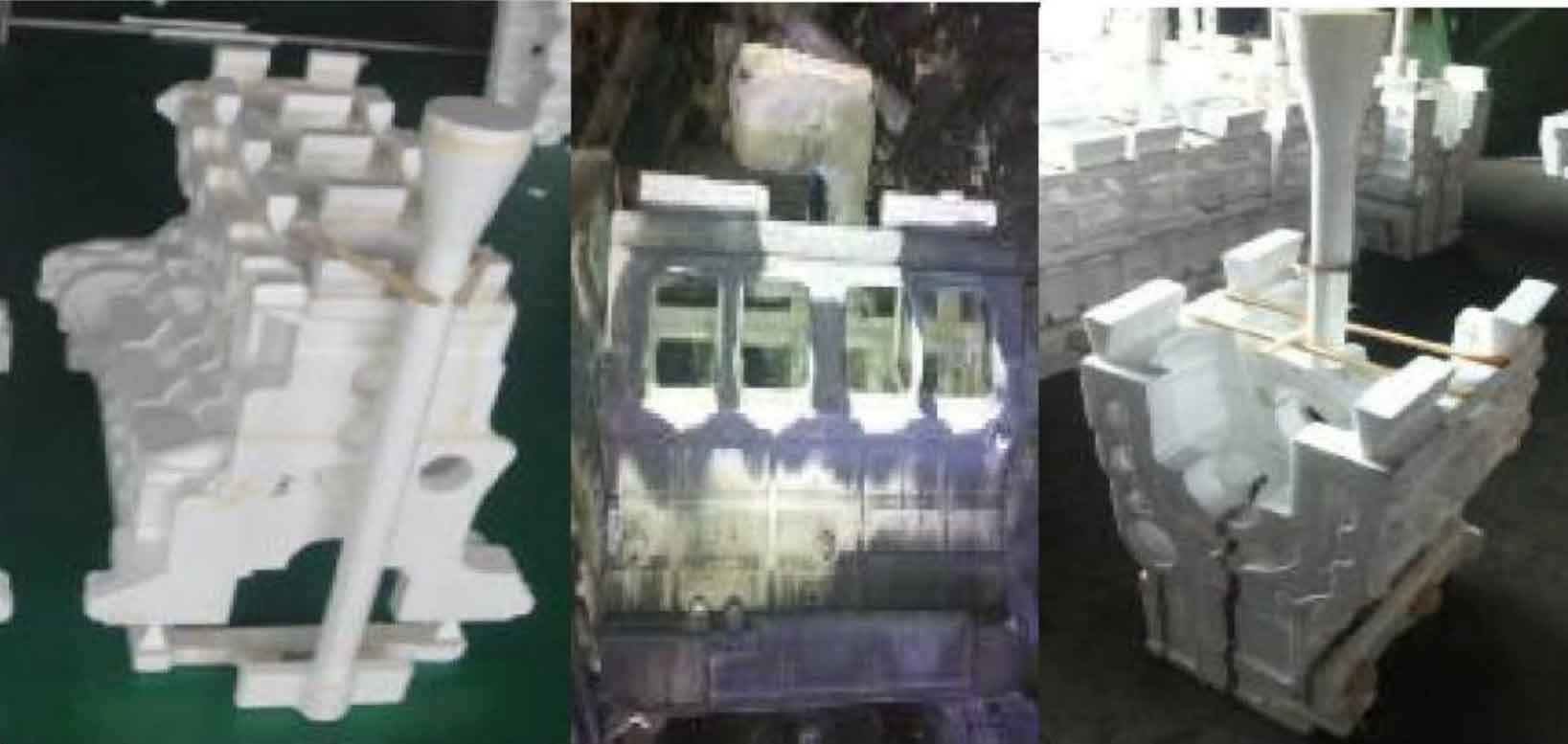
Gao Chengxun and others used lost foam casting technology to form low alloy cast iron four cylinder engine cylinder block. Figure 1 shows the pattern of lost foam casting and the form of gating system. Figure 2 shows the low alloy cast iron four cylinder block casting, with a yield of more than 95% and a process yield of more than 90%.
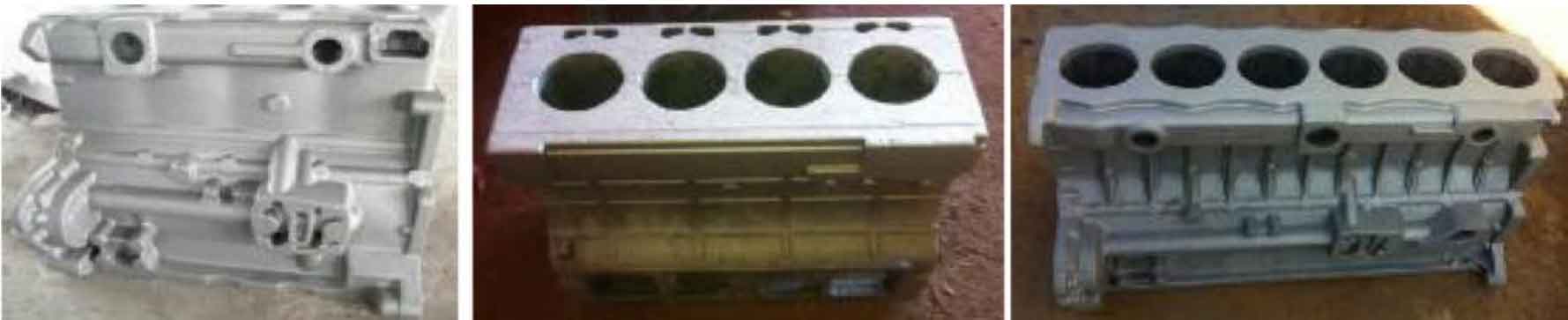
A company in Shandong uses lost foam casting to form a six cylinder engine cylinder block by horizontal side bottom injection process, as shown in Figure 3, for large-scale production.
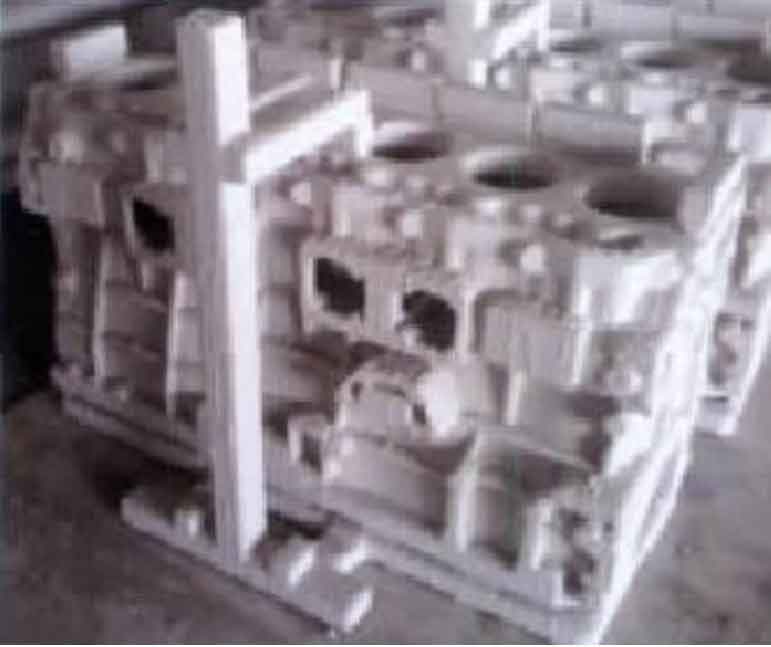
The United States has the most mature technology for producing automobile cylinder block using lost foam casting technology. In 2001, Saginaw foundry of GMPT began to use lost foam casting technology to mass produce automobile cylinder block. Saginaw foundry is the most advanced and largest lost foam casting factory in the world to produce automobile cylinder blocks. Figure 4 shows the lost foam casting pattern and formed castings of six cylinder engine in Saginaw foundry.
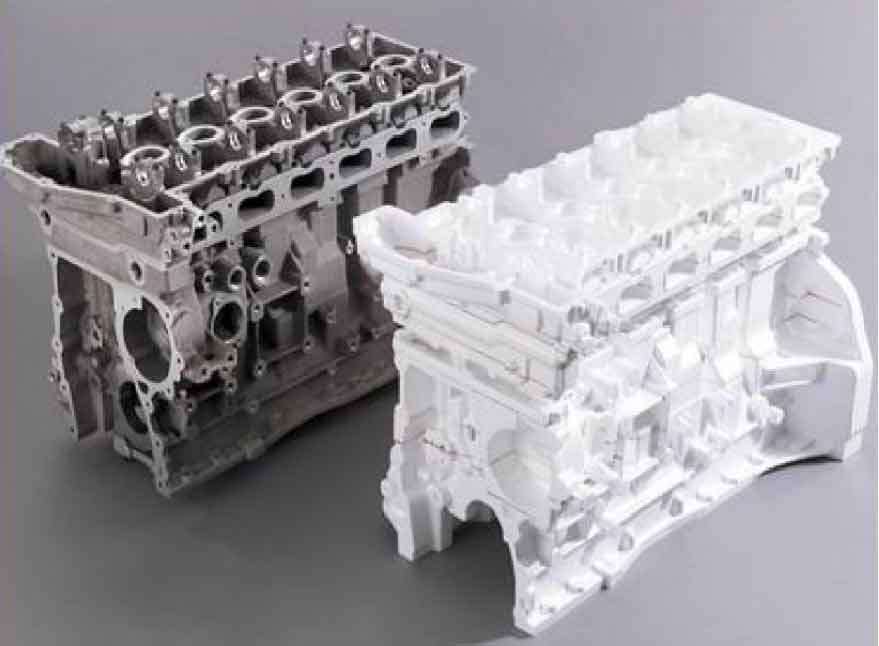
Lost foam casting technology, especially for manufacturing automobile engine cylinder blocks, is a sophisticated and advanced process. Here’s an overview of how it works:
- Pattern Creation: The first step involves creating a foam pattern of the cylinder block. This pattern is usually made from polystyrene foam, which is identical in shape and size to the actual metal part to be created. The foam pattern is slightly larger than the metal part to account for the metal shrinkage during cooling.
- Assembly: The foam pattern is then assembled into a cluster, if necessary, depending on the size and complexity of the final cast. For complex structures like engine blocks, multiple foam pieces may be glued together.
- Coating: The foam cluster is then coated with a refractory material, like ceramic or similar, which will form the mold. This coating must be strong enough to maintain its shape and withstand the temperature of the molten metal.
- Compaction: The coated pattern is placed into a flask and surrounded by unbounded sand. The sand is then compacted around the pattern to provide additional support during the pouring of the molten metal.
- Pouring: Molten metal is poured directly into the flask, where it replaces and vaporizes the foam pattern. The heat from the molten metal burns away the foam, leaving behind a cavity in the shape of the cylinder block.
- Cooling and Solidification: After pouring, the metal is allowed to cool and solidify. During this time, the sand holds the shape of the cast.
- Shakeout: Once the metal has solidified, the sand mold is broken away from the cast part. This process is known as shakeout.
- Finishing: Lost foam casting may require finishing processes like sandblasting, grinding, or machining to achieve the final dimensions and surface finish.
Advantages of Lost Foam Casting for Engine Blocks:
- Precision and Complexity: Allows for the creation of complex shapes with precise dimensions, which is critical for engine blocks.
- Reduced Waste and Cost: Since the method can create near-net-shape castings, there’s less waste of material and reduced machining costs.
- Improved Surface Finish: Generally provides a better surface finish compared to traditional sand casting.
- Design Flexibility: Engineers can design more intricate parts without worrying about mold parting lines.
However, there are also challenges, such as controlling the quality of the foam pattern and ensuring the integrity of the refractory coating, which are critical for producing defect-free castings. This technology is widely used in automotive industries for its ability to produce lightweight, strong, and complex parts efficiently.